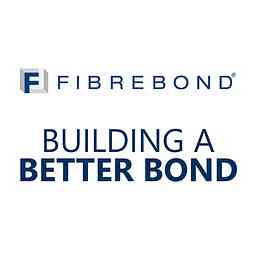
Keeping Workers Safe During COVID-19 with Martee Gonsoulin
16m
·
Building a Better Bond by Fibrebond
·
To support the nation’s critical infrastructure, Fibrebond couldn’t shut down during the pandemic. Halting operations, even for a short period, was not an option.
Fibrebond’s Vice-President of Supply Chain and Manufacturing Support, Martee Gonsoulin, said the company had to act quickly to put procedures, safeguards and practices in place to ensure worker safety so that business could continue during COVID-19.
“Early on, Louisiana was one of the hot spots for COVID-19," Gonsoulin said. "So, back in February, we began to dive in and look at the details of what would be needed to combat the pandemic, and, by the end of February/early March, we put in place policies we felt needed to happen to keep our folks safe.”
Fibrebond continued to get policies and procedures in place through March before Louisiana's March 30 stay-at-home mandate. Gonsoulin credited her 20-plus years in pharmaceutical manufacturing for providing insight and much-needed experience in preparing for this unforeseen event.
“All of the sudden, some of the background I have with dealing with the FDA, CDC and pharmaceutical science really played into my helping shape and draft policies to help employees feel safe here," she said.
What were some of the measures Fibrebond took to keep its employees safe?
“We have many employees in production who work in close quarters with other people,” Gonsoulin said. “We knew we had to put measures in place to keep those folks as safe as possible and continue to support customers and the infrastructure.”
From temperature scans for every employee or person entering the facility to health questionnaires, isolating employees to specific buildings, staggered work shifts with zero interaction between shift changes, face coverings for all employees, and outdoor breakroom setups, increased designated restrooms and work-at-home policies for most administrative and professional staff, Fibrebond left no stone unturned in its mission to make worker safety priority No. 1.
The episode Keeping Workers Safe During COVID-19 with Martee Gonsoulin from the podcast Building a Better Bond by Fibrebond has a duration of
16:06. It was first published
More episodes from Building a Better Bond by Fibrebond
Keeping Workers Safe During COVID-19 with Martee Gonsoulin
To support the nation’s critical infrastructure, Fibrebond couldn’t shut down during the pandemic. Halting operations, even for a short period, was not an option.
Fibrebond’s Vice-President of Supply Chain and Manufacturing Support, Martee Gonsoulin, said the company had to act quickly to put procedures, safeguards and practices in place to ensure worker safety so that business could continue during COVID-19.
“Early on, Louisiana was one of the hot spots for COVID-19," Gonsoulin said. "So, back in February, we began to dive in and look at the details of what would be needed to combat the pandemic, and, by the end of February/early March, we put in place policies we felt needed to happen to keep our folks safe.”
Fibrebond continued to get policies and procedures in place through March before Louisiana's March 30 stay-at-home mandate. Gonsoulin credited her 20-plus years in pharmaceutical manufacturing for providing insight and much-needed experience in preparing for this unforeseen event.
“All of the sudden, some of the background I have with dealing with the FDA, CDC and pharmaceutical science really played into my helping shape and draft policies to help employees feel safe here," she said.
What were some of the measures Fibrebond took to keep its employees safe?
“We have many employees in production who work in close quarters with other people,” Gonsoulin said. “We knew we had to put measures in place to keep those folks as safe as possible and continue to support customers and the infrastructure.”
From temperature scans for every employee or person entering the facility to health questionnaires, isolating employees to specific buildings, staggered work shifts with zero interaction between shift changes, face coverings for all employees, and outdoor breakroom setups, increased designated restrooms and work-at-home policies for most administrative and professional staff, Fibrebond left no stone unturned in its mission to make worker safety priority No. 1.
How Data Centers Became Even More Critical than Expected in 2020
The data center industry was expecting 2020 to be a year of growth, said Hector Moreno.
But Moreno, the Director of Business Development, Data Centers at Fibrebond, and his colleagues had no idea just how much growth that would be.
The coronavirus pandemic sent everyone into their homes, with work, school and play all relying on home connections that ultimately relied on data centers firing on all cylinders. The projections for the year were going to be blown out of the water.
“I think as soon as the pandemic hit, a lot of their acceleration and demand validated those initial plans,” Moreno said. “From a macro level, it’s really increased everybody’s pressure to build. In this space, there’s always sort of a push-pull, cart before the horse, if I build it will they come or just build it just in time, but our customers really want their space as soon as possible.”
It’s a trend that seems unlikely to go away any time soon, even as regulations meant to stop the spread of COVID-19 begin to lift. With companies like Fibrebond benefiting from the work-from-home tools they set up prior to the pandemic and seeing things go well as most employees put in their hours remotely, there may be a shift toward requiring less time in the office.
That will require data centers to keep improving and perhaps getting even closer to customers.
“Absolutely. I think 100%. I think that you can count on,” Moreno said. “When we’re talking about moving from 10 to 5 milliseconds of latency, it’s a big difference. Companies that have strong WiFi networks in their facilities or strong fiber networks don’t really have this issue, but one of the issues coming out of this is, now, you have families putting a huge strain on us. So how do we get to that market?”
MegaMod is the Next Big Solution for Customers in the Oil and Gas Industry
What do you do when boomtown and processing location are hundreds of miles away? If you’re Fibrebond, you devise a solution that involves floating a building with a name reminiscent of the Transformers down the Red River.
It’s another example of how the business is looking to accommodate its customers’ needs.
With liquified natural gas exports booming along the Gulf Coast and the recent discovery of natural gas, oil and natural gas liquids in the Permian Basin, customers have been looking for the best way to power their processes.
MegaMod from Fibrebond gives them an option for single-piece building delivery, improving on previous iterations.
“The key difference between MultiMod and MegaMod is that it’s obviously a lot bigger,” said Chet Carpenter, Fibrebond’s Business Development Manager. “The other is the delivery method. These, obviously, once they’re put together, can’t go down the road. (With) a MultiMod, each module is small enough to get on a truck, go to a site, get pieced together there and then integrated.
“The MegaMod goes down the river, which is the only viable method of transportation once it gets this big, and ends up somewhere along the coast.”
Why go big? In Carpenter’s eyes, there are three reasons.
“There’s really a ton of benefit there with a building that shows up fully assembled as opposed to one that shows up with multiple pieces needing to be assembled on site, so I would say efficiency, quality and even safety are three major factors, there,” he said.
Not only does it keep on-site labor costs low, but it reduces the possibility for leaks and other issues that may pop up with multi-segment delivery.
There’s little doubt that MegaMod is a big solution for customers along the Gulf Coast.
How Fibrebond's Industry Expertise Makes for Deeper Client Relationships with Chase Cook
Fibrebond has solutions in several different markets; gensets, data centers, power, telecom, and more. With that diverse reach, it's critical for the company to not spread itself too thin and maintain high quality products and service regardless of the job. What is their secret sauce for pulling it off?
On this episode of Building a Better Bond, we're joined by Chase Cook, who brings solutions to building client relationships at Fibrebond. Cook is the Director of Business Development for Fibrebond's Power division; he brings his diverse industry knowledge to Fibrebond to help the company position themselves as the industry’s experts.
Relationships are a huge part of what Fibrebond does, and Cook said they have the experience to simplify projects their clients want to build. On this episode, he went into a little history of Fibrebond in order to explain where they are now. He said they used to be a telecommunications company but have expanded to oil, natural gas, packing generators, and more; with all the different things they are involved in, Cook said it now allows them to drive the power, data, and telecommunications segments together to strengthen their position in the market.
Oil and gas companies had record numbers last year and Texas had a record year as well, supplying 41% of the total oil and natural gas in the US. Cook said that the technical sales team sees over one billion dollars in sales every year. He said that because of the high volume of business they are able to look through their data to find out what is most important to clients and consumers. Cook said that Fibrebond has been in business for 38 years, and they are known for taking a unique approach in their business partnership.
Changing Materials, Maintaining Mentality with Randy Bogan
Many industries can change, some seemingly overnight. Others can take years to complete their makeover. On this episode of Building a Better Bond, Randy Bogan, Warehousing Director for Fibrebond, sat down with Sean Heath to discuss the nature and rate of change in the industry.
The nature of business is change, but that helps a company grow, according to Bogan.
“You have to really be on your toes, now," he said. "There’s a lot going on daily. Time flies by. It’s very, very busy, and it’s just a lot going on with the product lines that we have.”
After leaving the company for several years, although there may have been several product changes, the sense of family was there the moment he returned, Bogan explained.
“We all like each other," he said. "We get along, because we know that, in order for Fibrebond to succeed, everyone has to succeed and do their job and do it correctly.”