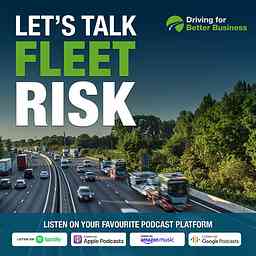
Let‘s Talk Fleet Risk
by Driving for Better BusinessA podcast for those who manage drivers and their vehicles, and want to reduce road risk in their organisation. drivingforbetterbusiness.com
Copyright: Copyright 2021 All rights reserved.
Episodes
Managing the transition to fleet electrification
30m · PublishedFor Q2 of 2022, Driving for Better Business is focusing on sustainability so it seems a great idea to invite Paul Kirby onto a special edition of the Let’s Talk Fleet Risk podcast. Paul is one of the best-known experts on electric LCVs with over 30 years in the automotive sector. He’s one of the founders of the EV Café and can be seen advocating for electric vans at many of the commercial vehicle shows and conferences. Paul is also the founder of consultancy and training firm EV Essentials.
https://www.drivingforbetterbusiness.com/podcast/episode/managing-the-transition-to-fleet-electrification/
Useful links
EV Café https://www.evcafe.org/
EV Essentials https://www.ev-essentials.com/
Paul Kirby https://www.linkedin.com/in/thepaulkirby/
DfBB Article: Electric vans and your ‘driving for work’ policy (10/10/2019) https://www.drivingforbetterbusiness.com/articles/electric-vans-and-your-driving-for-work-policy/
Transcript
Simon: Welcome to Let's Talk Fleet Risk, a podcast for those who manage drivers and their vehicles and want to reduce road risk in their organisation. This quarter 2, Driving for Better Business is focusing on sustainability, so it seems a great idea to invite Paul Kirby onto a special edition of the Let’s Talk Fleet Risk podcast.
Paul is one of the best-known experts on electric LCVs with over 30 years in the automotive sector. He’s one of the founders of the EV Café and can be seen advocating for electric vans at many of the commercial vehicle shows and conferences. Paul is also the founder of consultancy and training firm EV Essentials.
Welcome to the podcast Paul.
Paul: Thank you very much Simon
Simon: Paul you’ve got something in common with our other podcast guest this month, National Grid Fleet Manager Lorna McAtear – you were both crowned Green Fleet Champions at last year’s Green Fleet Awards. What’s fired up your passion for electric vehicles, and especially electric vans.
Paul: I first drove a Mercedes Benz sprinter electric vehicle in 2004 and when you think about how long its taken for that vehicle to get here it’s incredible, but really, having driven electric vehicles over the last 20 years, what I’ve noticed is that they are such a better environment to be in and when I was working at LeasePlan the company became a member of the EV100 which is a group of businesses all committed to Net Zero by 2023 and the that sort of passion grew to help people. When I saw the environmental benefits, I also saw the driver benefit because I am a great believer in positive mental health and helping people to have a good experience in their vehicles. When you think about the driver behind the wheel of a van they often have a bad reputation but the main reason I believe for that is the stress and pressure they are under in terms of deliveries etc. Electric vehicles take a lot of that away – it’s a much better experience for the driver and ultimately, I believe electric vehicles are safer to drive than their diesel or petrol counterparts. So, there’s a number of reasons, but’s it is focused on getting the job done in a safer more efficient fashion that’s good for the driver.
Simon: You talked about the fact that electric vehicles are safer – why do you think that?
Paul: Having driven vans of all shapes and sizes over the years, if you’re sitting behind the wheel of a diesel vehicle with a gear stick and you’re trying to pull out into a busy roundabout, let’s be honest, vehicles are operating in busy city centres or towns, pulling out from junctions with various loads on, and what the electric vehicle gives you is a point and shoot. You don’t have to worry about changing gears or being in the right gear - you can put both hands on the steering wheel and go, whereas in the diesel vehicle you’re having to do a number of things. You could be in the wrong gear for the weight in the back etc. That was the first thing and also, we drive more carefully in an electric vehicle because we’re conscious of preserving range, I think we’re more relaxed. A study was done on London taxi drivers that said they were happier, which is interesting, they were calmer and more focused on the wheel of an electric LEDC range extended electric vehicles. They were delivering a much better experience and so those are the main reasons I believe it’s safer to driver an electric vehicle.
Simon: The driver wellbeing is interesting – we’ve done a lot of work with CALM – van drivers are predominantly male, and CALM is aimed at preventing male suicide. It can be a very lonely existence - so making that environment nicer – and the electric vehicles are certainly pleasant places to be – so it’s probably an underestimated benefit.
Paul: I agree with you completely, CALM – the campaign against living miserably – I love that acronym. It’s such a ‘does what it says on the tin’ kind of description. I love that and the charity’s focus. When you think about the suicide rate of men it’s the biggest killer of men under 40 I think and men are our predominant driver population so the fact there are wellbeing benefits – it points to getting the drivers engaged early on in any approach we take to electric vehicles because they will understand the benefits.
Simon: The other point in terms of being safer to drive, when I spoke to Lorna who runs one of the biggest fleets in the UK, I’d expect her transition to electric vehicles to have seen possibly an increase in collisions as people go used to a new experience. Her experience was that people were more cautious and drove more safely and making sure that the charge lasted as long as possible they drove more safely, and her collision rate went down. Is that your experience?
Paul: Yes, what we know is that the vehicles are typically easier to drive, and drivers are calmer – that whole ecosystem works well. Insurers are even saying that you’re 25% less likely to be involved in an accident in an electric vehicle and this experience mirrors everything that Lorna has said. I wouldn’t disagree with any of it – it’s absolutely the case. Anybody I’ve come across driving electric vans are finding it a positive experience. But I will say getting the driver engaged in the first place will make or break that transition. We also hear stories when vehicles are demonstrated and drivers take them out into the big wide world, they are nervous – they say it doesn’t work – 1. Because it’s different, 2. Because they have to do things differently and charging becomes an issue because if you have only ever driven a petrol or diesel vehicle and you’ve only ever turned up at a petrol station to get your fuel, you may have never noticed the funny looking boxes with cables, that will power your vehicles, so you go into it with trepidation, so I think getting them onside in the first place is critical to a successful transition which will ultimately benefit the vehicle and the driver.
Simon: I know that some really big fleets are on their journey to complete electrification of their fleets by anywhere between 2025 and 2030 but it seems, there’s a lot of small businesses who don’t really know how to start. They maybe have a small fleet of diesel vans – what should they be thinking about – what are the challenges they need to think about now in order to transition as a smaller fleet to electric vans?
Paul: I think smaller fleets are slightly more challenged than the larger fleets as they tend to have predictable journeys and routes and mileage. They also have professional teams of fleet managers and probably experienced board members, finance execs, facilities people – all of those stakeholders who are needed for this transition. So, I think smaller businesses, if I take my own experience of stepping into business myself, there are a lot of questions you don’t know the answer to. There’s a lot of help out there – online and potentially people can come and talk you through the process, but you need to engage with a wider stakeholder base, starting by talking to landlords – you might say why? – but you talk to them because you need to think about charging. It’s the first thing to consider. You need to put in your own charging points, you’re not going to be reliant on the fuel station down the road. You will be putting in charging infrastructure in your own car park, premises – because we would want to be in maximum control of our own destiny when it comes to charging. Charging in the public domain at the moment is still somewhat of a concern because you can’t always guarantee you get on the charge points, and you can’t always guarantee they’re working. It’ s okay for most of the time, and it’s okay for a car – but when you’re in a van there are other challenges, so getting control of the charging experience is one of the first things you should do, almost before you think about vehicles. Can I charge whatever I buy? That’s the first question. Then you can start thinking about the vehicles and when you do, then it’s considering the data behind what you’re doing. I’m not a great fan of data, I’m a great fan of insight that data is essential for, but because I’m not a the most detailed of people I enjoy the opportunity to take data and then to turn out an answer than says these were the routes you have done, this is how many miles, this is where you’ve been and by the way if you put a charger here it would enable you to get additional charge in the place
National Grid - Net Zero by 2030 - Spotlight on Sustainability
27m · Publishedhttps://www.drivingforbetterbusiness.com/podcast/episode/national-grid-net-zero-by-2030-spotlight-on-sustainability/
Transcript
Simon: Welcome to Let’s Talk Fleet Risk – a podcast for those who manage drivers
and their vehicles and want to reduce road risk in their organisation.
My guest today is Lorna McAtear. Lorna is the fleet manager for National Grid – Hello Lorna and welcome to the podcast
Lorna: Thanks Simon. It’s great to be here.
Simon: Since we started this podcast last year Lorna you were one of the people I really wanted to talk to, but before I say why, could you start by just giving us a quick overview of the size of the National Grid fleet and the types of driving your staff are engaged in.
Lorna: I joined National Gird 2.5 years ago – we had 3000 vehicles on the fleet, 1700 company cars – only 7 were electric vehicles, so we’ve been on a massive transition through that. We have over 1000 commercials of which 350 are 4 x 4 and more recently, part way through last year we merged with WPD, so in total now we have 9000 vehicles, of which there are an awful lot more 4x4s and a few helicopters, so the transition is a large fleet now to manage.
Simon: We’re publishing this podcast in May 2022 and one of the reasons I wanted to have you on as a guest is that we’re putting the spotlight on sustainability. Driving for Better Business campaign is promoting a series of resources as well as case studies of fleets that have reduced fuel use and emissions – through either reduced mileage, more efficient driving or electrification of the fleet. You’re one of the best known advocates for electric vehicles and reducing emissions. National Grid as a company is aiming for Net Zero by 2050 – how does your fleet strategy fit into that?
Lorna: That was one of the first things I did – to design that fleet strategy and interestingly I was pushing the fleet strategy for a 2030 target when the legislations was for 2035 so there were a few challenges around why I was picking that date, but I think when you’re close to the marketplace you can see where the changes are coming in. I put together the plan for the next 10 years – knowing what I can control within in it. The 4x4s I mentioned, I know I can’t do anything about that. I can retrofit but there isn’t anything really, I can do for the vast majority on fleet, so it’s planning for a date in 2024 or 2025 knowing when the changes are going to happen. So, what I had to do is work with the enablers – what were the education programmes I needed to put in, that whole communication piece around it, which vehicles could I tackle immediately, which vehicles did I look at later – and just map put for everybody so we knew exactly when and where things were going to change. All I’m doing now as the years go by is sense checking into that original plan and working out whether I’m behind or ahead and is there anything else I can now do because of innovations that have come to market. Can I change some of my commercial vehicles earlier than I planned? There’s a whole raft of things that went into that but the key was having the plan in the first place and getting buy in.
Simon: Are you trying to replace the fleet vehicle sin line with your natural vehicle replacement cycle?
Lorna – Absolutely. You don’t need to get rid of the vehicles straight away. Just follow that replacement cycle so the whole plan was geared around that we mapped out every single replacement ad some of them have got checkpoints on so the heavier the vehicle is or the more ancillary equipment it has, it just a checkpoint in time and it may be t at actually we extend that vehicle because the different vehicle will come out later, so each time I have a replacement it triggers a conscious decision on are we replacing, or are we intending to do something different?
Simon – presumably helicopters present a challenge in their own right
Lorna – haven’t got a clue on that yet!
Simon: From a driver competence point of view, I had a week in one as part of a campaign we were running and there are some obvious differences, such as what you would check, and the driving characteristics – there are some obvious differences involved in driving an EV from the pre-use check angle as well as driving characteristics.
How does National Grid communicate these to drivers and how you liaise with colleagues responsible for driver safety on the training requirements for EVs?
Lorna: Stories are great aren’t they. The one thing is obvious is they are automatics. The first time I drove an electric personally was a Peugeot van and I nearly stuck my bosses head through the windscreen because I never driven a automatic before, so you learn from experience, and you can use those stories to relate to people. Its’s how you get that communication out there, and it’s how you normalize things. There are a lot of things we do with our ICE vehicles that don’t change even if you you’re in an EV. You’re still doing your normal drivers checks, tyres, make sure your windscreen wash levels are topped up, the FLOUR acronym, and we had some real challenges. Most of our EVs went onto the fleet during full lockdown during COVID so we had to do a lot of the driver education through peer to peer talks, through actually standing outside the vehicle and explaining things. There was a lot of online things because you’re right, understanding that regen you really can’t explain it to someone until they felt it themselves and they feel that vehicle so it’s just trying to work out pretty much with the whole sustainability plan what can you do, when can y you do it, which drivers adapt easily, some of the drivers already had EV cars so an EV van wasn’t a problem. So how do you identify your higher risk drivers and then make sure that each of the education pieces are there. What we did was a lot of hand holding to start with because it was new to us. It was new for us to educate others. We weren’t sure what education we needed. You’ve always got challenge – they can get uppity if you want to give them some education so it’s how you go about that.
Simon: How do you deal with an incident like a breakdown, or a collision – when things are different with an EV. Unless you’ve been told you might expect to be able to do certain things…
Lorna: Again. Some of that is already in our policy anyway, some of the base policies – fleet managers should check all the base policies and reinforce those because you’ll find an awful lot of it already covers those nuances between the EVs and you’re using breakdown providers, they know what they can and can’t do. So one of the things I did on that, when I was at Royal Mail and we’re doing it here – when we’re doing mass rollouts we notify the breakdown provider in that location so they can gear up to make sure that provision Is there. But what I am finding is that they don’t breakdown!
Simon: Well, that’s handy
Lorna: They’re far better – you have far less mechanical issues. Less moving parts, people drive them better, more cautious to start with as well, it’s quieter so the indirect benefits are people’s wellbeing. Drivers are less stressed out, the old fashioned ‘white van man’ goes, people are interested in how you’re looking after the environment, so the public perception is better for the drivers as well, all those things make for a better wellbeing type of environment, and it all comes into how they driver the vehicle.
Simon: I was wondering if you’d seen any changes in collision levels with the EVs? Are drivers more prone to collisions, maybe as they get used to the vehicles, or have you not seen a difference? Sounds like you’re not seeing that.
Lorna: We’re not seeing that at all. It helps that you can’t get a replacement EV so don’t damage it in the first place! We are seeing drivers look after those vehicles better so we are seeing less incidents. Don’ forget they come with a lot more safety features as well
Simon: They have pretty much a full suite of collision avoidance tech as a whole?
Lorna; Vans always used to be the poor relations to the cars, there’s a lot of that tech coming in now – blind spot indicators, a lot more coming in to the vans with the EV tech.
Simon: One of the primary challenges with electric vans has been reduced load carrying capacity due to the weight of the battery, which can lead to over loading. Has that been a problem for NG?
Lorna: No, because we before we put them in, we did that assessment of the specification and used it as an opportunity to reassess how you do the job. You’re not taking what you did before and just replicating it. You’re taking it as an opportunity to say what can I do differently. Can some of that kit come out because when you look at it you realise the kits has ended up in the vehicle over they years and it’s become habit. When you go into it you don’t need it – you find you’ve been hoarding stuff. So you just change the way of working and have a look at the vehicle and go back to basics. Because we knew we could not get EVs in the larger sizes when we first started, we looked at the vehicles and said – what do you actually need? If we put the ladders the site instead, can you reduce the weight? There was a lot of work in designing specifications first to make sure that everything came in as it should.
Simon: It’s a great lesson for any fleet – it illustrates the need for const
Overcoming the hurdles to good driver safety management
33m · PublishedJohn Andersen is the National Logistics Director for Tarmac, and manages one of the largest supply chains and fleets in the UK, working across the rail, road and water sectors.Tarmac operates a mix of vehicle types. In this podcast John talks about communicating the risks to his drivers effectively, and overcoming the hurdles to good driver safety management.
https://www.drivingforbetterbusiness.com/podcast/episode/overcoming-the-hurdles-to-good-driver-safety-management
Useful links
Tarmac Case Study https://www.drivingforbetterbusiness.com/case-studies/business-champion/tarmac/
Transcript
Simon: Welcome to Let’s Talk Fleet Risk – a podcast for those who manage drivers
and their vehicles and want to reduce road risk in their organisation.
With me today is John Anderson. John is the National Logistics Director for Tarmac and manages one of the largest supply chains and fleets in the UK working across the rail, road and water sectors.
John, Tarmac operates a mix of vehicle types. To start with could you give us a breakdown on the size of fleet you operate, and the type of driving the business needs to manage
John: As market leaders in the construction industry, we manage materials supply. As a major supplier to the UK infrastructure, we manage a fleet of around 5000, half of those are large goods delivery vehicles but also 2500 are light commercial vehicles or cars and vans which our employees use to travel to and from their place of work.
Simon: That’s a complex fleet to manage. What have been your main challenges in identifying areas for improving driver safety and how have you met those?
John: We risk categorise each of those and we focus on the large goods vehicles. We cover in excess of 50 million miles per year making hundreds of thousands of deliveries per month. As such, these vehicles work on site, on the public highway, and offsite as well, so there’s a whole range of risks associated with this, not just the physical risks but also the behavioural and psychological risks around operating these vehicles. Our initial focus is around some of the generic issues – speeding, around harsh braking, control of the vehicle and we make sure that we are satisfied that the people operating these vehicles are competent to do so
Simon: Do you get any driver input into what the actual risks are with the different types of transport movements?
John: We do, we try and engage heavily with the drivers. I think this is a very valid point. Historically our engagement and involvement with the drivers tended to be around negative events, and I think it’s a real reflection and something that’s been part of the Driving for Better Business approach. Historically our involvement with drivers was a result of a negative event – an incident, an accident a road traffic collision or a speeding event, whereas now we are really broadening that, and I think it’s something that COVID has bought to the forefront. So, ‘hang on a second, these people do million of miles in their daily lives, representing our brand and delivering our products and are very much customer facing’ so we realise we have to engage with them. We make a conscious effort to engage in a positive way and make sure that communication is 2-way – so monthly newsletters for example, we really celebrate some of the small things these people do to deliver successfully and be part of our brand, and make sure that they have the ability as part of the delivery system to report good acts as well as negative acts – so near hits or near misses, they can submit that electronically from their vehicle and we look to give them recognition on the positive events as well. Drivers are on our health & safety committees and in our site liaison meetings. We involve them in the discussions and our plans and future thoughts.
Simon: So getting drivers to report near misses must have been quite a challenge. They have to feel they’re properly supported form the top, or else there’s a risk they feel they are reporting something that will get them into trouble. You must have done well with the driver culture to get them to feel comfortable reporting near misses – that’s great as it gives you more data to work on to make them safer.
John: I think you’re right. That’s a been a fantastic success. First of all we automated it – made it easy and initially we made them anonymous but actually we find people put their names, sites, locations and are proud to say they are part of that campaign. If they see something is not working, they step in and again no one wants a negative outcome. One of our key foci is whether they’re driving, in an office, on a machine or on a customer site and they see something that has potential to cause harm, they make a conscious decision to report it and I believe they now realise it makes them feel better about themselves and better about working for our organization.
But there’s no doubt it’s been a challenge and there’s no question that culture was there, but once you get over that it’s about the safety element and people’s wellbeing, I think that starts to gain traction and we see that grow every month. Then you make data driven decisions. Those data driven decisions make sure your strategy and your policy are heading in the right direction and aligned to where the real challenges are about people who drive for a living.
Simon: What’s the secret to communicating your key risks effectively with the drivers to try and achieve that?
John: I think if we go back to the year before COVID, 2 years before COVID, we had a big campaign where we went out, we had stickers, various giveaways for our hauliers and drivers and we went out to our sites and offices and spent time actually talking and listening – again it was trying to be proactive rather than reacting to a negative event. We launched it and advertised it and, in the end, people were nominating and requesting us to go to their sites to meet and talk about some of their concerns. People were very proud about some of the things they had done, the best practice, and they wanted to show it off and we encouraged the transport teams, the distribution teams, the depot & warehouse teams to get out there and talk to the people who are representing us every day, get on the front foot and listen to them and that really has driven that collaboration forward, and got them to a position where trust in the senior leadership team, in the people they deal with every day is important. We certainly would advocate the quickest way to build trust is to get in front of your people and talk to them – and listen That’s important. My motto is ‘you said, we did’ – it’s important that if we agree to do something we do it, and they can see that, so that certainly starts a journey and is something you can build on.
Simon: That’s obviously a good example of how you communicated to the drivers – there’s basically clear standards set that the drivers understand that they need to follow, they understand why, they’re trying to follow these standards and to maintain high levels of professionalism with their driving. You touched on the fact that it’s important to recognize the good. Can you give us examples of how you recognize good behaviour in practice, and how do you provide feedback when someone has fallen short?
John: We employ our own drivers, and we also have third party contractors so we engage with the key people in that organization as well as the individuals driving the vehicle. We do get regular reports from LinkedIn or Twitter, through communication, through social media channels and we make sure someone in a relatively senior position will pick up the good feedback and speak to the haulier and make sure they speak to the driver, Quite often, myself I will often drop that driver an email or a phone call to say we’ve had a report that you slowed down for some horses and we got really good feedback from those riders, ‘the Tarmac Trucker was the most considerate driver they’d passed’ – and that’s great feedback and we send that to the driver and the employer but also to the local site, and I think again trying to promote that local ownership and recognition that driver s representing them and the brand and who we are as a logistics function.
So some good opportunities to celebrate success there. There are small tangible things they get a body warmer or a fleece or a cap – just some small things.
On the negative side, we recognize people make mistakes or misjudgments, it is making sure we don’t overly penalize that but that people are aware they have gone wrong, why it’s important that they rectify that and we put measures in place that we’ve had that discussion, we’ve implemented that action. But it’s following up on it. We know that some of the biggest risks are when things are not followed up and it creeps up and becomes a repetitive event and that’s something we revisit with the help of some of our technology – and hopefully we prevent a recurrence.
Simon: With Tarmac being such a large organization and, with a supply chain working under the Tarmac banner that also contributes to a significant number of transport movements, I’m wondering how you ensure the various layers of management within Tarmac, and your suppliers, understand and meet the standards that you’ve set?
John: Again, it is complex, there’s no question. We supply hundr
Could you save £56k with a Road Safety Framework?
36m · PublishedJoining us in this episode is Dave Conway, Road Safety Manager for FM Conway.
https://www.drivingforbetterbusiness.com/podcast/episode/could-you-save-56k-with-a-road-safety-framework/
Useful links
FM Conway Case Study https://www.drivingforbetterbusiness.com/case-studies/business-champion/fm-conway/
Health & Safety Event – April https://www.drivingforbetterbusiness.com/driver-safety-zone-2022/
Transcript
Simon: Welcome to Let’s Talk Fleet Risk – a podcast for those who manage drivers and their vehicles and want to reduce road risk in their organisation.
Hello and welcome to the March edition of Let’s Talk Fleet Risk.
With me today is Dave Conway who is the Integrated Management systems and road safety manager for FM Conway.
Hi Dave and welcome to the podcast
Dave: Hi Simon
Simon: That’s quite a mouthful for a job title – can you explain more about what that role entails and how you got into road safety for FM Conway.
Dave: My role is to look after the business management systems of the company – I was looking after quality and environmental systems and somewhere along the way road safety systems came along as a certifiable framework standard.
I got involved and I became beyond passionate about it – it’s now a large part of my job and we changed my job title to reflect that.
Simon: So you’re not a fleet manager or driver manager – you’re all about setting up the systems and processes that manage that road risk.
Dave: Exactly that – and I’m a great believer in systemic solutions to most problems and safe system is the key particularly with road safety. That’s really where I come from. It does mean I actually have the advantage of being independent of transport and logistical operations which enables me to take a better view on how they are doing things and come at a problem with a different viewpoint without having to worry about normal business considerations.
Simon: Just give us an idea of the size of the fleet that Conway operates – and what sort of vehicles they are
Dave: These days I think our fleet – and it’s changed a lot over the past 2 years – is around 1100 vehicles, ranging from an HGV fleet of about 400 vehicles and those HGVs could be a low loader, an articulated loader or an articulated tanker vehicle right down to 4 wheeler and 6 wheeler tippers. We then have a fleet of about 550 vans and about 80 company cars or grey fleet – and by grey fleet I’m talking about cars that are privately owned but funded by the business to do mileage on behalf of work. So that’s the breakdown. It’s a little bit of everything. If it hasn’t got wings, we tend to drive it.
Simon: Because that’s such a mixed fleet, I guess there’s a number of different people within the organisation, the people who all have an impact on road safety – fleet managers, driver managers, operations managers, transport managers for the HGVs etc. How do you work with the fact that responsibility gets shared across so many job roles – how do you ensure that everyone understands what’s their responsibility is?
Dave: The whole point of the systems, the management systems is so that everyone can follow process and procedure, regardless of whether they are running a couple of lorries or running a patch up operation on a street somewhere in town, or whether they’re running bulkers around the M25 delivering aggregates or bitumen. If everyone is working to the same management system, we can ensure consistency in terms of our output and we can ensure everyone is following the same safety standards and doing the best we can – that’s the approach.
Simon: Was that challenging – to get everyone pulling in the same direction?
Dave: It’s not so much challenging to get them pulling – no-one gets up in the morning wanting to kill people on the roads or anywhere else. However, they have different priorities – they want to get their job done. They want to be as efficient as possible with their work and so on. So, the challenge is understanding their other priorities whilst getting them to follow road safety management systems. I think as long as you can be empathetic to their other issues you can deal with it – at the end of the day the best system is one that everybody wants to follow. If it’s easy to follow they will follow it so it has to be a system that is easy to follow and works for everybody.
Simon: And is that something you asked for feedback on when you were designing these systems? How important is it to get feedback from others in the company when you build these processes?
Dave: It’s imperative. You’ll have a framework for your standards, and you’ll know what has to be in there but when you’re going to work out how you’re going to do it the people who are expert in doing it – or perhaps in not doing it – are those people on the ground. It doesn’t matter if it’s a quality system or an environmental system you have to speak to the people doing the work and say “this is what we’re trying to do – how would you do it?” Then you can come to a consensus and find the best useable methodologies and put them in place – there’s no point in putting in place something that is not going to happen anyway.
If it needs to be policed, it’s not working. If it’s the right way to do it, they are going to do it because it makes sense without policing.
Simon: So, did you get driver input into those systems as well?
Dave: Essentially, throughout. When we started establishing our 39001 system, we set up a working group and to this day it’s in place – we have people from the board, from management and drivers – drivers and supervisors – and they all sit on this committee to make sure all of their thoughts are allowed for.
Simon: So, you mentioned ISO39001 and I know you’re a big advocate for that. Why did you choose that as standard that Conway was going to embed in the business?
Dave: ISO390001 is a management system framework standard for road traffic safety. It’s been our experience and indeed the world’s experience that certified management systems work. They make a difference, there are demonstrable benefits for everybody and very few downsides.
How we got into it – it’s an interesting story. We received a letter back in 2012, Transport for London were one of our key customers and we received a letter from Sir Peter Hendy CBE who was the commissioner for Transport for London. He had commissioned a piece of research by the Transport Research Laboratory into why cycle crashes in London seemed to be dominated by construction industry vehicles. He sent us this 700-page report and it came up with a number of recommendations – and we were asked to support the recommendations. One of those was adopting a formal framework management system for your transport operations such as ISO 39001 and that was the point we embraced it.
I hadn’t heard of it – so I went and bought the book, and we did it – not realising that we would be the first. I’d spent most of my working life railing against some aspects of health and safety saying ‘why were we so worried about some aspects at work when you were more likely to die driving for work or driving to and from work?’ and all of a sudden here was a system that was supporting everything that I was saying and I embraced it with a passion – and here I am still doing that.
Simon: You were one of the first business to get ISO39001 accreditation and you did it 2012 – obviously you’ve had that in the business for close to 10 years now – so what has been the benefits to FM Conway that you can categorically say – that’s because we had that management system in place
Dave: I am always mindful of the fact that if you are going to persuade a business to adopt these systems there needs to be a business case. I really can’t overstate the business case. Within the first year of adopting the system, we found ourselves with a £56,000 reduction in our fleet insurance premium. That sum of money paid the certification for 39001 for the next 7 years. There’s your business case – if you’re running a system like that you will have less accidents. You will have less crashes, less injuries, less costs on maintenance, you’ll find that your drivers drive better and if they drive better there’s less wear and tear and less fuel usage. From a business point of view – absolutely amazing it will make money – simple as that. It will not cost you money.
There are a lot of road safety systems out there and I’m not going to quote other systems, but I can tell you from experience they will cost a small fortune. I speak to a lot of people in business, and they say we don’t have enough budget as we are a member of this other scheme and it costs us so much we can’t afford training let alone anything else.
39001 will not cost you money. Yes, there will be some costs, but I promise you you’ll get every penny back through business improvements and that’s the fundamental reason for having a system like that.
Simon: What types of vehicles you run and the number you’ve got – it’s a sizeable mixed fleet. What are the challenges in running that fleet that you think your management standards help with. If you’re not running a management standard like that what ar
Van Safety Ratings - how safe are your vans?
28m · PublishedThis month's episode of the Let's Talk Fleet Risk Podcast is all about Advanced Driver Assistance Systems (or ADAS for short). ADAS covers all the collision avoidance systems and driver assistance technology that can help prevent a collision or minimise the severity in the event that the incident can't be avoided altogether. Joining us in this episode is Matthew Avery, who is the Chief Research Strategy Officer for Thatcham Research. Matthew discusses the importance and benefits of using ADAS in commercial fleets, as well as the results of Thatcham Research's latest round of safety tests on commercial vans
https://www.drivingforbetterbusiness.com/podcast/episode/van-safety-ratings-how-safe-are-your-vans/
Useful links
Thatcham Research: https://www.thatcham.org/ Euro NCAP Commercial Van Safety Ratings https://www.euroncap.com/en/ratings-rewards/commercial-van-ratings/ Commercial Van Safety Ratings 2020 https://www.drivingforbetterbusiness.com/articles/how-safe-are-your-vans/
New Van Safety Ratings - how safe are your vans? https://www.drivingforbetterbusiness.com/articles/van-safety-ratings-how-safe-are-your-vans/
Transcript
Simon: Hello and welcome to the February edition of let’s talk fleet risk which, this month, is all about Advanced Driver Safety Systems, or ADAS for short.
ADAS covers all the collision avoidance systems and driver assistance technology that can help avoid a collision or minimise the severity in the event it can’t be avoided altogether. It’s a subject I’m personally fascinated by, and I’ve monitored how these systems have developed over recent years.
With me today is Matthew Avery who is the Chief Research Strategy Officer for Thatcham Research.
Hi Matthew and welcome to the podcast
Matthew: Hi Simon
Simon: Matthew – perhaps you could start by giving us a brief introduction as to why ADAS is important, how Thatcham is involved, and what your role is?
Matthew: Sure – Thatcham is a not-for-profit UK Insurance research centre and we’re members of Euro NCAP – I’m sure many of the listeners will know Euro NCAP – it’s 25 years old now and has been leading the charge to getting information to the consumer for them to buy a safer vehicle.
Since about 2014 we have really pushed the fitting of advanced driver assistance systems that help avoid the collision in the first place, and we’ve moved on from crash testing to seatbelts and airbags and the ability to avoid having the collision in the first place.
Vehicle manufacturers have been fitting technology – cameras and radars – on vehicles to detect what’s around them, respond to a potential collision threat by automatically putting brakes on and steering away from the collision. It’s very effective technology and we’re seeing it really working. We’ve now got a huge amount of standard fit in AEB technology and its reducing crashes by about 35% so it’s really good technology. It’s there not only to protect yourself but it’s also there to protect other road users and vulnerable road users. These systems will detect cyclists and pedestrians and other vehicles and [preventing a life-threatening collision. We saw this technology working so we began to broaden our scope in 2018 and looking at other vehicle types. Thatcham undertook research which showed the huge void there is between passenger cars and vans. We have a huge amount of standard fit on passenger cars – and vans from the same manufacturer have almost no technology fitted at all.
A good example is Nissan – we looked at the Nissan Duke and that has standard fit lane support systems, advanced driver systems, radars, speed limiters. Great technology – a 5-star car. When we look at the NV400 which is the Interstar at the same sort of price – absolutely no technology available at all, not even as an option and we thought there’s no reason for a manufacturer who makes the equipment, not doing that.
So, we started our first ratings in 2020 of commercial vans to highlight to the public and to fleet operators, to owner drivers and to large fleets – you must have this technology fitted. You have it on your cars, you should have it on your vans – where much of it is simply not available, choose another van. Where it is available as a cost option make sure that as an operator, you’re ticking those boxes to protect you and your driver and your brand.
Simon: So, I wanted to talk specifically today about ADAS on Vans. ADAS on cars has been developing quickly for over a decade now and we’ve reached a point where there are some fairly advanced systems available, and in order to score highly on the Euro NCAP safety ratings, most cars now have many of these systems fitted as standard. But that isn’t the case with vans, which have been much slower to adopt the technology – why is that? Why don’t they put that ADAS technology onto the vans?
Matthew: We think most of it is just down to consumer pressure and economics – manufacturers understand the power of the NCAP 5-star rating – and if you do not have 5 stars or 4 stars, you’re unlikely to appeal to a broad market. We see that with vehicle manufacturers, so they strive to get the 5-star rating, whether that’s Renault or Volvo or Mercedes Benz. Every manufacturer strives for the 5-star rating.
But as there wasn’t a similar rating for commercial vans, there’s only the regulations which did not require any ADAS fitting so manufacturers are thinking why do I need to fit it? If I can make my van cheaper and more competitive then I will do that. Some broke the mould – Mercedes was producing a lot of optional equipment and VW on their Transporter range was beginning to fit AEB as standard and we saw a market drive for that. Hence the need for the ratings to tell the consumer which van to buy.
Simon: You’ve been working with Euro NCAP to create this new safety rating system for vans so users can clearly see what systems are available and how good they are. In December 2020 you released the first set of results from tests on 19 common models of van in the UK – what did you find?
Matthew: We were shocked by what we found. Most ADAS systems aren’t fitted as standard – VW were fitting some of it as standard – but most of it including the best-selling van in the UK – Ford Transit Custom – just had none of this equipment as standard.
Some manufacturers were fitting it as an option, but there were quite a lot who weren’t even doing that – I mentioned Nissan – so we tested 19 vans and obviously a lot of these are shared – so Stellantis badge the same van in different markets, whether it’s a Fiat or a Peugeot or a Citroen, but it’s essentially the same van off the same production line.
We decided to rate in separate categories, so we have a platinum rating and there no platinum ratings, then gold – and then silver and bronze and then a not-recommended and there were too many vans that were simply not recommended. That was our first set of ratings and best performers were VW and from Ford with their large transit and the Mercedes Sprinter – those were our best performers then, but we were hoping we would see some manufacturers rising to the challenge, and this year we have.
Simon: What was the response from the vehicle manufacturers and fleet managers to those results?
Matthew: It was mixed. Vehicle manufacturers recognised this – they said we are making the right plans for the customers, and therefore there is not so much of a requirement from customers to buy this and can we really afford to make our van less competitive than another van by putting this safety equipment on?
When we talked to them, they said ‘we do have this technology – and we could fit it if there was a demand.’ We see Euro NCAP driving the demand – so the message to the fleet operators is you can’t afford to not have your vehicles on the road earning money and even after a minor collision they could be off the road being repaired – and the potential injuries for your drivers – and think about your brand reputation as well. Nobody wants to see a sign written van involved in a collision on Facebook or Twitter, so there’s lots of reason why you should be buying a van with this equipment. Our ratings make the choice clear – buy this van with this equipment and you’ve got the safest van on the market.
Simon: What’s the thinking behind the different type of safety rating to the cars – the Euro NCAP car ratings 5 star is the top whereas with the vans you’ve opted for bronze, silver, gold, platinum…
Matthew: There’s a couple of things – we wanted to separate it. We got a different message to a different audience. It’s a B2B message – we are trying to talk to fleet operators and owner drivers and they’ve probably, on their drive, they’ve got a 5 star Euro NCAP vehicle to protect themselves and their families – do they do that for their drivers?
So we’re talking to a different audience and we wanted to separate it. The other thing is this is a series of tests that we will change every couple of years so we will continue to raise the barrier and also we wanted to see this as a badge of honour so we’ve been engaging with a lot of traffic auth
Safe loading - where do fleet operators get it wrong?
33m · PublishedWelcome to the first podcast of 2022. The Driving for Better Business Campaign is focussing on loading issues this month, so we asked Nina Day from the HSE to join us for this episode. Nina has worked for the HSE for 21 years. She’s a chartered mechanical engineer and a dangerous goods safety advisor specialising in road and workplace transport.
https://www.linkedin.com/in/ninaday/
https://www.drivingforbetterbusiness.com/podcast/episode/safe-loading-where-do-fleet-operators-get-it-wrong/
Useful links
Driving for Better Business Resource Library
Driving a van: weight limits and loading https://www.drivingforbetterbusiness.com/resources/search-results/?res=Driving+a+van%3A+weight+limits+and+loading&id=9896
Load security: good practice https://www.drivingforbetterbusiness.com/resources/search-results/?res=Load+securing%3A+good+practice&id=9896
Load security: roles and responsibilities https://www.drivingforbetterbusiness.com/resources/search-results/?res=Load+securing%3A+roles+and+responsibilities&id=9896
Load securing: vehicle operator guidance https://www.drivingforbetterbusiness.com/resources/search-results/?res=Load+securing%3A+vehicle+operator+guidance&id=9896
Load security: consequences of poor load security https://www.drivingforbetterbusiness.com/resources/search-results/?res=Load+security%3A+consequences+of+poor+load+security&id=9896
Load security: how DVSA enforces the rules https://www.drivingforbetterbusiness.com/resources/search-results/?res=Load+security%3A+how+DVSA+enforces+the+rules&id=9896
Ratchet straps: What you need to know https://www.drivingforbetterbusiness.com/resources/search-results/?res=Ratchet+straps%3A+What+you+need+to+know&id=9896
Securing loads on flatbed vehicles https://www.drivingforbetterbusiness.com/resources/search-results/?res=Securing+loads+on+flatbed+vehicles&id=9896
HSE Website https://www.hse.gov.uk/
HSE Driving and Riding Safely for Work guidance https://www.hse.gov.uk/roadsafety/
Van Driver Toolkit
Safe Loading https://vandrivertoolkit.co.uk/
Loading: Know Your Limits https://vandrivertoolkit.co.uk/
Transcript
Simon: Welcome to Let’s Talk Fleet Risk – a podcast for those who manage drivers
and their vehicles and want to reduce road risk in their organisation.
Welcome to the first podcast of 2022. The Driving for Better Business Campaign is focussing on loading issues this month, so we asked Nina Day from the HSE to join us for this episode. Nina has worked for the HSE for 21 years, she’s a chartered mechanical engineer and a dangerous goods safety advisor specialising in road and workplace transport.
(transition)
Simon: Hi Nina – welcome to the podcast.
Nina: Thanks for inviting me – it’s great to be here.
Simon: Now, Nina, I know that safe loading is right at the top of HSE’s list when it comes to work related road safety. At DfBB we focus on commercial vehicles and HGVs tend to be heavily regulated but vans less so. What regulations apply to each vehicle category in respect of load safety?
Nina: Well, the regulations are the same regardless of the size of the vehicle, so it doesn’t matter if it’s an HGV or a passenger car – it’s the same legislation. We have section 48 of the road traffic act, regulation 100 of the constructions use regulations and they both say the load has to be secured to prevent someone being injured. There’s also the workplace safety aspect. If you’re an employer or you’re a self-employed person whose work covers other people which covers a lot of people in transport, then you have legal responsibilities under the safe and healthy at work act and legislation to protect anyone who works for you, and also anyone who could be at risk because of your work, so that’s wide ranging. These are 2 separate areas of law, but they do overlap. The responsibilities overlap quite a lot and it’s the same regardless of the size of vehicle.
Simon: So, what are the common problems that you see where fleet operators get this wrong and you see unsafe loads? When the regulations are ignored, what do you see on the roads?
Nina: The fundamental problem where an incident has happened – usually a fatality or a serious injury – it’s a lack of risk assessment or the risk assessment is so inadequate it may as well not have existed. That’s something I’ve seen in the vast majority in load shift incidents I’ve worked on in the last 15 years. There are a lot of misconceptions on risk assessments – but it doesn’t have to be bureaucratic and time consuming. It’s just thinking through what you do, what could go wrong and what how to stop someone getting hurt if it does go wrong. HSE provides a lot of free guidance on our website. If you haven’t thought things through, the chances of everything else being right are actually quite low. All the other issues we see follow on from not having the risk assessment right. It’s also a legal requirement so if you’re an employer or self-employed, you do need to have a risk assessment.
The other issues I see a lot are people using the wrong load securing for the load they are carrying. Load securing equipment that is damaged or old and worn and not fit for purpose, or not using enough load securing. There’s no specific method – it’s up to you depending on the load you are carrying and the vehicles you are using. Whatever you do you must secure the entire weight forward and half the weight to the sides and rear. That is a minimum and if you secure to that level the load should stay where it is in an emergency stop, if you have to swerve to avoid a child, anything like that – the load should stay where it is.
A big issue at the moment is open vehicles, whether that smaller drop side type up to big tippers because people don’t appreciate that loads can move upwards and when that happens loads can be thrown off the vehicle.
About 5 years ago a lady was killed when a piece of work equipment that weighted about 60kg bounced out the transit pickup and struck her as she and her husband were walking on the pavement. That item should have been secured and it wasn’t. It bounced up so high it cleared the height of the sides and came of the vehicle.
Only last year a man was killed when a chunk of stone that only weighed 8kg bounced of the vehicle and came thorough his car windscreen,. He was driving with his wife and grandchildren and killed instantly. No one sets out to kill anyone like that. I think one of the most difficult things I’ve ever read over the last 15 years in looking at load shift incidents was in a statement from a driver who had been involved in an incident and he started off by saying ‘I never set out to kill anyone’. But if you’re operating an open vehicle you need to make sure that load is properly sheeted, properly tied down, properly covered, big items tied down so they can’t bounce out. Don’t assume that the sides by themselves will stop the load from coming out.
Now, I think the last point I want to make is that when you’re loading a vehicle you’ve got to make sure it’s not overloaded. Its very easy to do with vans and smaller vehicles. Just be aware of what your vehicle is rated for and what you can put in it. When I’m out with the police and the DVSA I see a lot of overloaded vehicles. If you overload the vehicle if you don’t distribute the load evenly across the load bed that will affect the handling of the vehicle. It might increase the braking distances or make it more likely to roll over so it’s really important to think about how you load it and make sure you’re not overloading it.
Simon: Brilliant, so to dig in a little bit deeper into a couple of those points. We were talking about items in an open back LCV or a tipper truck that can jump out. You could go over a pothole or a speed bump, or anything – I’ve seen that happen as well. One of the things we’ve quite often seen come out of compliance checks, trucks where all the big stuff is secured properly, so plainly they know what they are doing, but then they throw a few last minute items in the back, a bucket of bolts, a generator, a shovel. They know what they’re doing but they just haven’t done it with the last bits. One of the worst things we saw were a couple
Driver Fatigue: Not just a tick box
34m · PublishedShow notes
I’m joined today by fatigue expert Dr Paul Jackson of Fresh Air Training
Paul is a Chartered Psychologist specialising in human performance and has assisted safety-critical organisations to implement fatigue risk management systems for over 20 years in a career that has also included positions as
- Research Manager at the Department for Transport responsible for looking at impairment resulting from fatigue, drugs and alcohol
- Visiting Lecturer in driver fatigue at Cranfield University
- Head of Impairment Research at TRL
Paul was an expert witness in last year’s landmark legal case, in which the Office of Rail and Road successfully prosecuted an employer for health and safety breaches, as a result of two of its employees being killed in a road traffic collision where fatigue was identified as the primary cause.
This successful criminal prosecution demonstrated that having policies and procedures on fatigue management is not enough.
In this podcast, Paul and I discuss:
- The events leading up to the crash,
- What the company did wrong and why it was prosecuted,
- The key lessons for employers to take away from this case,
- And where to start when looking at fatigue management.
https://www.drivingforbetterbusiness.com/podcast/episode/driver-fatigue-not-just-a-tick-box/
Useful links
Driving for Better Business Article on the case.
https://www.drivingforbetterbusiness.com/articles/company-found-guilty-after-driver-fatigue-death/
Driving for Better Business ‘fitness to drive’ resources
https://www.drivingforbetterbusiness.com/resources/search-results/?section=325&category=Fitness%20to%20Drive
ORR press release on guilty verdict
https://www.orr.gov.uk/search-news/contractor-renown-consultants-ltd-guilty-after-two-died
ORR press release on sentencing
https://www.orr.gov.uk/search-news/contractor-renown-consultants-fined-ps450k
Transcript
Simon: Welcome to Let’s Talk Fleet Risk - a podcast for those who manage drivers and their vehicles, and want to reduce road risk in their organisation. I’m joined today by fatigue expert Dr Paul Jackson, of Fresh Air Training. Paul is a chartered psychologist, specialising in human performance, and has assisted safety critical organisations to implement fatigue risk management systems for over 20 years in a career that has also included positions as Research Manager at the Department for Transport, where he was responsible for looking at impairment resulting from fatigue, drugs and alcohol; Visiting Lecturer in driver fatigue at Cranfield University; and as Head of Impairment Research at TRL. Paul was an expert witness in last year’s landmark legal case, in which the Office of Rail and Road successfully prosecuted an employer for health and safety breaches, as a result of two of its employees being killed in a road traffic collision where fatigue was identified as the primary cause. The successful criminal prosecution demonstrated that having policies and procedures on fatigue management is not enough. In this podcast, Paul and I discuss the events leading up to the crash; what the company did wrong and why it was prosecuted; the key lessons for employers to take away from this case; and where to start when looking at fatigue management.
(transition)
Simon: Hi Paul - welcome to the podcast. Paul: Good afternoon.
Simon: We’re going to talk today about a double fatality due to driver fatigue that ultimately lead to the successful prosecution of the company that employed the two who died. Now, Zac Payne was a trainee welder who was just 20 years old. He worked for a company called Renown Consultants, and was driving a company van at the time of the crash. He had his 48 year old colleague, Michael Morris, sat next to him in the front of the van. Now, Paul, you were involved in that case as an expert witness. The outcome should have significant implications for employers. I was wondering if perhaps you could start by just giving us an outline of the events that led up to this particular crash.
Paul: Sure. So, the events that led to the renowned prosecution occurred on the night of the 18-19 June, back in 2013. In the early hours of Wednesday 19 June, the two welders you mentioned, Zac Payne and Michael Morris, were killed when their van - the van they were travelling in - crashed into an articulated lorry, which had been parked in a lay-by on the A1. They had been on their way back to Doncaster, after a night shift in Stevenage, in Hertfordshire. The previous day, the day before the incident - so that’s Tuesday 18 June - Zac Payne had driven another Renown crew up to a place to Alnmouth in Northumberland. He’d left Doncaster, where the depot was, at 4:15 in the morning, and that crew arrived at around 7:30 in the morning, and waited for the job to start. But for various reasons, that job was cancelled, and so Zac Payne then drove the crew back to Doncaster, arriving at around 3 in the afternoon. In the meantime, an urgent job had come in which required two more welders for a job near Stevenage - a place called Langley Junction. And that job was going to happen on the 18-19 June - so that Tuesday night/Wednesday morning.
The company, Renown, allocated Michael Morris as the senior welder. And the only person they could find as the assistant was Zac Payne. So, they were allocated to do the job, and they set off for Langley Junction at around 7:15 in the evening. Mr Morris was driving, and they arrived at Langley Junction at around 9:45 in the evening. They had to wait to take possession of the railway, and that happened from around 11:15. They completed their tasks, and then set off on their journey home, just after 3:30 in the morning. And this time it was Zac Payne who was driving. At around 5:30 in the morning, the van had been travelling north on the A1, and straight off the carriageway to its near side, and into a lay-by where the articulated lorry was parked. Their van hit the articulated lorry and unfortunately, tragically, both Michael Morris and Zac Payne were killed. At the time of that collision, Zac Payne - the driver - had been up for around 26 hours.
Simon: So, in this case, the prosecution was brought by the Office of Rail and Road, rather than the Health and Safety Executive. but Renown were still prosecuted under the Health and Safety at Work Act. So, could you just explain what it was they were actually prosecuted for please?
Paul: They were prosecuted on three breaches of health and safety regulations; the 1974 Health and Safety at Work Act, and the 1992 Managing the Safety of the Workforce Act. So, the first breach was failure to manage the fatigue of their workforce. Secondly, for exposing employees and non-employees to the risk of injury arising out of fatigue. And thirdly, for failing to make a suitable and sufficient risk assessment before these two particular employees were sent out on that night shift.
Simon: So, fatigue was clearly identified in this case as the primary cause of these Fatalities, but, in the rail industry, fatigue is well known as a risk because they’ve got a large workforce that are often operating at night because that’s when the tracks are free for maintenance or they’re doing shift work. So what went wrong in this case on the management side? Did they have a system for managing fatigue?
Paul: They had procedures. They had, I suppose, the rudimentary elements of a fatigue management system. Certainly they were not without procedures. The procedures they had included a policy - a fatigue management policy, procedures for assessing the risks associated with fatigue, and particularly the procedure to authorise excess hours; so where somebody was being requested to work longer hours than normal, they had an authorisation form that was meant to be completed as a result of the risk assessment. What went wrong was that the company didn’t follow its own fatigue management procedures. In addition to that, they didn’t comply with the working time limits for safety critical work - such as welding - which require that there should be a minimum rest period of 12 hours between booking off from a turn of duty to booking on for the next duty. In addition to that, they didn’t conduct a sufficient and suitable risk assessment - particularly of the fatigue of Zac Payne, who as I mentioned had been awake for a considerable length of time even before starting this job.
Simon: You see a broad spread of attitudes, shall we say, among companies towards risk. Where, at one end you have a total disregard – don’t care, not interested in managing risk, just doesn’t register and all they care about is running the business, up to the other end, where managing risk is central to the business, and nothing happens unless it’s done the correct way. In the middle, you often have people who maybe want to do the right thing but maybe haven’t got the time or are under pressure, or they don’t have the experience to do it properly. Are you able to say where Renown’s management fitted on that scale?
Paul: Yes, and I think perhaps it’s bette
Driver wellbeing: How reward breeds success
27m · PublishedShow notes
Welcome to this edition of Let's Talk Fleet Risk - a podcast for those who manage drivers and their vehicles, and want to reduce road risk in their organisation.
In this episode, Simon Turner, Campaign Manager for Driving for Better Business, is joined by Phil Hitchen, the Managing Director of Belle Vue Manchester - award-winning and quality-branded transport provider.
Phil and Simon discuss
- The importance of driver personality to good service and maintaining high standards across multiple locations
- Reducing driver stress, and recognising and rewarding good driver performance
- Why awards are so important to the business, helping to drive a culture of consistent high standards
https://www.drivingforbetterbusiness.com/podcast/episode/driver-wellbeing-how-rewards-breed-success/
Useful Links:
Belle Vue website
https://bellevue-mcr.com/
10 Mistakes to avoid when procuring school transport
http://yellowschoolbus.co.uk/
Transcript
Simon: Welcome to Let’s Talk Fleet Risk – a podcast for those who manage drivers and their vehicles, and who want to reduce road risk in their organisation. I’m Simon Turner and I’m the campaign manager for Driving for Better Business – and my guest in this episode is Phil Hitchen, who’s the Managing Director of Belle Vue Manchester, an award winning and quality branded transport provider. In this episode, Phil and I discuss the importance of driver personality to good service and maintaining high standards across multiple locations. We talk about reducing driver stress and recognising and rewarding good driver performance. And finally, we look at why awards are so importance to the business, helping to drive a culture of consistent high standards.
(transition)
Simon: Hi Phil, and welcome to the podcast.
Phil: Morning Simon! Pleasure to be here.
Simon: Phil, most businesses only have to worry about the risks to their drivers or other road users, yet your vehicles are generally full of customers as well, which could be quite a daunting challenge. What’s your view on work-related road risk at Belle Vue?
Phil: I think from a transport point of view… if you train your people right, your drivers right, do your safety checks and health and safety announcements, and show passengers what to do in the event of an emergency… I think if that comes second nature and ingrained in the way they just reel it off every job… I think if your maintenance team follow the operational guidelines and procedures, it just runs like clockwork and it’s no fluke that your insurance claims records stay low, your MOT pass rates stay at 100%, when it comes to vehicle inspections… the traffic commission and DVSA alike with their inspections every 6 weeks; we like to do ours every 4 weeks because we operate from an ethos of ‘a stitch in time saves nine’ and it keeps the fleet running at optimum level.
Simon: So what’s the biggest challenge you think you face in running a safe service for customers?
Phil: I think in 2019/20/21, it’s evident there’s a shortage of PCV and HGV drivers in the UK. I think we’re quite proactive on training drivers to basically meet a service charter which requires things (to be a little higher standard) than the average. We have to recruit more numbers now to get the quality of driver we want, whereas 10 years ago they’d come flooding through the doors, you’ve got a nice fleet, you pay good wages, you’re a nice company to work for an youd look after your team. Right now, after a pandemic, coach drivers have gone into other trades… there is a huge shortage.
So for me, the biggest challenge at the moment, which has gone on for about 3 or 4 years since the CPC really kicked in, where elder drivers retired and didn’t want to go through the CPC, and there’s a shortage of young drivers coming through, so I think the biggest challenge to the industry and certainly our business is getting the right calibre of drivers through the door in the first instance.
Simon: And how do you then look at ensuring they’ve got the capabilities and the right attitude? How much effort do you put into driver assessment and training to ensure that they do deliver the level of service that you expect from them all?
Phil: We probably do a lot more than your average company, and we probably do some things differently than some of the top companies in the UK. My philosophy is we recruit personalities and we teach them to drive later. So, what we do is, straight from the offer and application form, we measure people’s personalities. Once that’s done, they do a driving assessment. If they get offered the position, they then do anything that could start from a 1 day to 5 day induction training, depending on experience. About 10 years ago, I knew our business could do a lot better, and I knew our drivers could drive better. I knew that as a business, the directors and the board and the management team could perform better – so we decided to put tracking systems on all of our fleet; what that did was tell us how drivers accelerate, how they brake and how they corner. We decided to use a system called Traffilog, because I perceive that to be the market leading system – National Express favoured that. Operators who work for National Express only seem to use the basics that National Express wanted to use, whereas we used everything. We literally drove peak performance driving, and then when we’d done that and we were saving copious amounts of fuel, which was about £63,000 per annum, we decided to use this personality tool to measure people so that we could get them to respond to passengers and give better service.
Simon: So with the tracking system then, that would typically give you a lot of data on driver behaviour – how much time do you spend analysing that data and how do you use that to improve performance and improve the service?
Phil: So, any bus or coach operation has key performance indicators. The accounts department, they have certain KPIs that they look at – the bank balance, the direct costs, the sales, the overhead. They’re always looking at their dashboard of figures. In operations – in tracking our drivers let’s say – we have people in compliance, whether it’s watching CCTV or watching the tracking system, we have people watching the idling times. Basically, it’s on a scoring system, and if you visualise a scoring system from 0-200… when we first set out, we had drivers averaging between 40 and 100, so 0-20 would be really good, it’s what we call “The A Team”. 20-50 is good, and 50-100 I class as average. Over 100-150 is inefficient, and 150-200 is technically dangerous. We made it company policy to get all our drivers under 50. When we achieved that, we had 1 or 2 stragglers, lurking around 60-70. And some of these guys were experienced, we’re not talking about somebody who’s just passed the PCV licence and is a bit of a novice. Just regarding accelerating, braking, and cornering. Imagine a coach going down a main road at 30mph, about a quarter of a mile away they see the lights turn to red – an educated driver will take his foot off the accelerator, cruise down to about 20mph, they’ll see the lights change and he’ll put his foot to feather the accelerator and he’ll build that back up. And if you imagine you saw a chart where people are driving erratically, it would go up in the air and then drop down when he brakes, it would go like a zig-zag. When you get tracking education into drivers, those sharp points become smooth ridges, like a wave on the ocean. And I had drivers saying to me, “…what are you going to teach me about coach driving – I’ve been driving 20 years”, and I say – this is science, let’s just go with it. They say “…well the girl who’s monitoring it doesn’t even have a PCV licence – what’s she going to teach me?”. And then suddenly they did get all these notifications about over-accelerating, cornering incorrectly, and braking. We educated them – we’d send supervisors and operations managers out with them. And literally in a 2 month period we’d get all our team under 50. Then we got a league table; we have a bus league, a school bus league, and a coach league. And what we do is we have £300 worth of prizes, so basically the top performing driver gets £150 a month, the second and third placed drivers get £75 each. And it’s not because of the money, but it’s a bit like soldiers – you’ve got Dad’s Army, the regular army, the paratroopers, the SAS… Coach drivers are the same. They want to be in the SAS. They want to walk in their driver room knowing they’re a top performing driver. When we got the league tables going – and it wasn’t just for the money, although that did influence people – they would compete with their colleagues to get the top scores, and that’s driving with a 0 score. That means no events, no harsh braking, no over-accelerating, and those KPIs that our compliance team see, if they go above the 20 which we class as ‘The A Team’, what happens is, when people are driving efficiently, they drive safer, passengers get a comfier ride, there are less roadside RTAs, there are more vehicles on the road rather than in the garage being repaired. If you invest in that system, and you invest in the right supervisors and compliance team tracking, drivers do perform better. When they don’t, you know there’s education/training to get them where they should be. And if they haven’t got the desire to improve, you replace them.
Simon: I love the idea of the SAS
NHS Hospital transport: a gigantic challenge
25m · PublishedShow notes
My guest in this episode is David Malone who is the Transport and Travel Advisor for The Newcastle upon Tyne Hospitals NHS Foundation Trust.
His responsibilities include setting and implementing the strategic direction for all hospital managed transport as well as all delivery transport movements to and from site.
This includes not just fleet vehicles, vans, pool cars and grey fleet but also car parking, park and ride, passenger transport services, taxis and couriers.
David also chairs two Best Practice Groups for the NHS National Performance Advisory Group - one for Transport and Logistics, and the second for car parking, sustainable transport and active travel policy.
In this podcast I’m going to be talking to David about how he manages such a wide range of transport activities including a grey fleet of almost five thousand and the challenges of driver communication with such a large workforce. We discuss the challenges around ensuring outsourced transport providers meet their legal obligations to manage road risk, and we look at how the Trust’s transport activities will need to develop in the future to meet their zero-carbon ambitions.
https://www.drivingforbetterbusiness.com/podcast/episode/nhs-hospital-managed-transport-the-challenges/
Useful Links:
Newcastle upon Tyne Hospitals declare climate emergency
https://www.newcastle-hospitals.nhs.uk/about/ambitions/climate-emergency/
DfBB resources for Grey Fleet
https://www.drivingforbetterbusiness.com/resources/search-results/?section=312&category=Grey%20Fleet
Transcript
Simon: Welcome to Let's Talk Fleet Risk - a podcast for those who manage drivers and their vehicles, and who want to reduce road risk in their organisation. I'm Simon Turner, and I'm the campaign manager for Driving for Better Business. And my guest for this episode is David Malone, who's the transport and travel advisor for the Newcastle-Upon-Tyne Hospitals NHS Foundation Trust. His responsibilities include setting and implementing the strategic direction for all hospital-managed transport, as well as all delivery transport movements to and from site. This includes not just fleet vehicles - vans, pool cars and grey fleet - but also car parking, park and ride, passenger transport services, taxis and couriers. David also chairs two Best Practice groups for the NHS National Performance Advisory Group; one on transport and logistics, and the second for car parking, sustainable transport and active travel policy. In this podcast, I'm going to be talking to David about how he manages such a wide range of transport activities - including a grey fleet of almost 5000 - and the challenges of communication with such a large workforce. We discuss the challenges around ensuring outsourced transport providers meet their legal obligations to manage road risk, and we look at how the Trust's transport activities will need to develop in the future to meet their zero carbon ambitions.
(transition)
Simon: Hi David. Welcome to the podcast.
David: Thank you very much. Thanks for having me on.
Simon: David - hospital trusts have a huge range of transport activities as part of their routine business operations. I was hoping you could start by just telling us a little bit more about your role - how many vehicles you're responsible for, and the different types of staff mobility and transport movements that a trust like yours needs to manage.
David: Okay, so in terms of the size of our organisation - we're one of the largest trusts in the United Kingdom, and we provide a huge range of specialties across the whole of the Northern region, and in some cases beyond. In terms of our fleet size, we don't have a huge in-house fleet. Mostly estate vehicles, catering vehicles and the like. The fleet itself is quite small - but we do run lease schemes. So we've got about 200 business cars out and about - so that's for community nursing provided across the region. But we also, as a result of that, have quite a significant amount of grey fleet - not so much to go out and visit the community but more for staff moving between the two major hospital sites we have. So in terms of fleet, we've got to be conscious of all that movement.
Then there's obviously the pressures of car parking. We've got 120,000 outpatients coming through the doors. We've got 16,000 staff. And I don't have 16,000 spaces. So we've got to try and accommodate all of those vehicles and all of those movements within approximately 3000 spaces between the two hospital sites. We have a large courier contract for moving all goods and specimens. So there's a lot goods and specimens moving, and in response to Covid-19 we've actually been delivering drugs to patients, to prevent longer queues within the hospital, or a need to travel in just for drugs. We also have a taxi contract, which we manage. And that's used a lot by staff patients as well. And then, in addition to all of that, we have our active travel, making sure that we're providing adequate cycle parking, bike-to-work schemes and the like. So we have to do all of that as well.
Simon: Yeah - it sounds like a huge role David. And I know when we've been talking previously, you told me that maybe a lot of the other trusts split these responsibilities across multiple people and departments. So, is there a benefit to you having it all controlled by one area of the organisation?
David: I think so and I've picked this up in my role as the chair of the NPAG groups that I attend - when transport's fragmented, if you've got different departments running courier and taxi and the likes, you don't have your eye on everything. And it ends up being a huge financial cost to the Trust, because there's replication of services. You've got individual departments or areas using different types of transport - and not always necessarily the right choice. So, to have it all brought under one roof, the benefit is we're very aware of the vast majority of transport movements and requirements for logistics and movement of staff etcetera within our organisation. And that helps us to make sure that we're choosing the right kind of transport, or managing costs. We're trying to keep everything joined together, and that has a huge advantage.
Simon: So with such a large remit then, what do you focus on most?
David: If I'm honest, car parking probably is about 10% of the role, but takes about 90% of my time - because it is so sensitive and contentious within the NHS. So car parking takes a great deal of my time. But most recently as well, we've introduced the new 'Driving at Work' handbook, so we've got to be aware of changes to the law and changes to the way things are going, to make sure the organisation is safe, and that our staff who are using these vehicles are safe, and correctly insured and mobile. So, the bulk of my time tends to be taken up on car parking, but I do focus quite a bit on how we're going to go forward with additional EV infrastructure. And we were the first trust in the world to declare a climate emergency - so there's a real drive at the moment to get our carbon emissions down, there's a lot of focus on the business miles that are being done; the trips that are being done to and from the hospital by staff, patients and visitors; and the use of our own vehicles as well.
Simon: You mentioned you got a new 'Driving for Work' policy - so presumably ensuring everything's done properly and your legal responsibilities are met is pretty important. What are the main challenges you face with the policy and that kind of thing?
David: If I'm honest with you, the main challenge we face with the policy is probably raising awareness. We have an organisation with 16,000 staff, there's a lot of cross-site movement, and it's making sure that where we do have staff who are using their cars for work - and that can be simple things from driving from one site to another, or going to a meeting in their car – understanding that is business use. And we've found ways of integrating them into parking policy, so no one will get a dual-site permit unless we've got confirmation that all of those checks have been done. And at the moment with our appraisal process - policies are being updated, and I'm integrating these changes into the appraisal process as well.
Simon: That's really good that you include it in the appraisal. So presumably driver communication is a key part of the role then. Hospital trusts, traditionally, are really big employers, aren't they? So, give us an idea of scale for the Newcastle Trust, and how big a challenge driver communication is, so that you can ensure standards are met across the whole workforce.
David: Well, the size of the organisation - we are one of the largest trusts in the UK. And we have 16,000 staff - a large number of staff who are using their vehicles for work - so, we have decided that the most appropriate way to make sure that we raise awareness of this policy, and raise awareness of staff responsibilities and organisation responsibilities to ensure the staff are safe, is to build into the annual appraisal process. Every member of staff is asked, as part of their appraisal, 'are you ever using your car for work, and if you are, you need to do X, Y and Z... and you must be aware of this policy', and the manager knows that those licence checks, those ins
Driver Distraction: An inconvenient truth
31m · PublishedShow notes
In this episode of Let’s Talk Fleet Risk, Simon Turner discusses the thorny issue of driver distraction with Dr Gemma Briggs from the Open University.
Gemma is an applied cognitive psychologist who has been researching driver inattention for over 15 years. She has lectured and written extensively on the attentional and perceptual issues caused by phone use when driving and has worked closely with several road safety charities to promote and share research findings.
Gemma and Simon discuss why a driver on the phone will suffer from 'inattention blindness'
What does the science say about our ability to multitask and take a call whilst driving
They look at the shared responsibility between employers and drivers, and their social responsibility to other road users, and discuss how management can often undermine the whole process.
Finally they look at some of the free resources that are available to help employers and drivers to understand and combat distracted driving
https://www.drivingforbetterbusiness.com/podcast/episode/driver-distraction-the-inconvenient-truth/
Useful Links
Driving for Better Business Resources on driver distraction and using mobile phones while driving
Search Results - Driving for Better Business
Driving change website: https://drivingchange.webflow.io/
Can you count the cars challenge: https://youtu.be/XRXdmmTk32I
The mobile office challenge: https://www.open.edu/openlearn/health-sports-psychology/psychology/are-you-driven-distraction
Video on distracted driving: https://www.youtube.com/watch?v=DzYAOOyVp7w&list=PLiUzMkrWK6CuyHzDV2ShdYEQgBYNC1N3B&index=2&t=8s this was linked to a brainteaser task (see attached) where people are asked to rate the behaviours in order of danger when driving.
The Inconvenient Truth About Mobile Phone Distraction: Understanding the Means, Motive and Opportunity for Driver Resistance to Legal and Safety Messages: https://academic.oup.com/bjc/advance-article/doi/10.1093/bjc/azab038/6262317?login=true
Transcript
Simon: Welcome to Let’s Talk Fleet Risk – a podcast for those who manage drivers and their vehicles, and want to reduce road risk in their organisation. I’m Simon Turner, and I’m the campaign manager for Driving for Better Business. In this episode, we’re going to discuss the thorny issue of driver distraction with Dr Gemma Briggs from the Open University. Gemma is an applied cognitive psychologist who has been researching driver inattention for over 15 years. She’s lectured and written extensively on the attentional and perceptual issues caused by phone use when driving, and has worked closely with several road safety charities to promote and share her research findings. Gemma and I are going to discuss why a driver on the phone will suffer from inattention blindness; what the science says about our ability to multitask and take a call while driving; we look at the shared responsibility between employers and drivers, and their social responsibility to other road users; and we also discuss how management can very often undermine the whole process. And finally, we look at some of the free resources that are available to help employers and drivers understand and combat distracted driving.
(transition)
Simon: Hi Gemma, and welcome to the podcast!
Gemma: Hi! Thanks for having me.
Simon: So Gemma, perhaps you could start by just telling us a little bit more about the type of research that you do.
Gemma: Sure. I’m a cognitive psychologist, and predominantly I’m really interested in how people pay attention, and how they perceive dynamic and changing scenes. The biggest application of that theoretical basis for me is looking at mobile phone use by drivers, so I’m really interested in what happens within a driver’s brain while they engage in a secondary task, such as having a conversation on the phone. I’m interested in what they do with their attention – do they try to divide their attention? Now research has looked into whether that’s actually possible or not – or whether – more likely perhaps – they shift their attention between those two tasks, and what that means for their performance in both tasks. How does their driving performance deteriorate? How does their performance in the phone conversation cope? How well do they cope with that situation – and what do they get out of it? What we’ve been able to share, which I’m sure we’ll talk about in more detail later anyway, is that it’s a really big problem in terms of driving performance. When we try to divide or shift our attention in this way, we can come unstuck.
Simon: Yeah. I doubt there’s anyone listening to this who doesn’t know that using a handheld phone while driving is illegal, but using a hands-free phone is legal. The implication of that for many is that hands-free is safe – or it wouldn’t be legal. So is it safer? What does your research show?
Gemma: Sure. So in research terms – it’s certainly not just my research or my collaborative research that’s looked into this – but what we do know is that hands-free phone use offers no safety benefit over handheld phones. So regardless of whether you’re physically holding your phone or not, you’re 4 times more likely to be involved in some kind of incident or crash. Your hazard perception ability vastly decreases. Your eye movements will change – so you’ll look around the scene less, and that can have implications for what you see and you don’t see. And those hazards that you do notice, you’ll take significantly longer to react to. So our research that I’ve done collaboratively largely with Graham Hole from the University of Sussex has looked into some of the specifics of that.
We wanted to identify – we know this is a problem, but why is it a problem? And it seems that it’s cognitive distraction that’s the issue. It’s not really whether you have both hands on the steering wheel and both eyes on the road ahead, because what we’ve been able to identify is that you can be in that situation – hands appropriately on 10 to 2 on the wheel and eyes looking at the road ahead – but if your mind is elsewhere, on a phone conversation, then you can miss things that happen right in front of your eyes. One particular experiment that we carried out put drivers in a driving simulator, and we tracked their eye movements. And we had this theory that perhaps the mobile phone conversation is drawing on cognitive resources that are actually needed for the driving task, and that’s why there’s a problem in terms of noticing and reacting to hazards. So, we asked some of our participants to complete a secondary task – a phone task, hands-free – which induced imagery. We asked them things like “true or false: in a rowing boat, a rower sits with his back to the front of the boat?”, “do cows have hanging ears?”. All of these kind of things that in order to answer, you probably have to conjure up an image in your head. We had another group of participants who weren’t distracted, and yet another group of participants who were distracted by non-imagery inducing statements – things that you either know or you don’t know, and they needed to verify. So, “the capital of Spain is Madrid”. Things that you probably don’t need to picture. And what we found was that it seems when people have a mobile phone conversation, they tend to picture their conversation partner; where they are, what they’re discussing, what they’re talking about, and you spontaneously create these mental images. The same brain areas that are needed for visual perception are also needed to create these mental images, and that can explain why a driver can look directly at something – and we know they’ve looked directly at it because we’ve tracked their eye movements – yet they’ve failed to react to it. When you ask them later, they say they didn’t see it – so in that particular experiment, those participants who were distracted by imagery inducing statements noticed far fewer hazards than any other participants. Those who were distracted by non-imagery were also worse than those who drove undistracted. But those distracted by imagery showed the worst performance overall. So, they either didn’t spot hazards, or if they did, they took up to a second longer to react to them, even if that hazard occurred right in front of them where we could demonstrate that their eye was directly pointed and trying to take in that information. It demonstrates a phenomenon known as inattention blindness; looking without seeing, so from that research – and we’ve built on that, and many others have done relevant work in that area – we can say that drivers on the phone, whether handheld or hands-free, can suffer from inattention blindness. They can look directly at things, yet not see them – and because they don’t see them, they don’t react to them.
Simon: So is that because the brain can’t physically hold two images at once? It can’t process the visual information from what’s going on in front of the driver at the same time as creating this mental image – it’s kind of one
Let‘s Talk Fleet Risk has 31 episodes in total of non- explicit content. Total playtime is 14:36:57. The language of the podcast is English. This podcast has been added on August 26th 2022. It might contain more episodes than the ones shown here. It was last updated on April 21st, 2024 00:12.