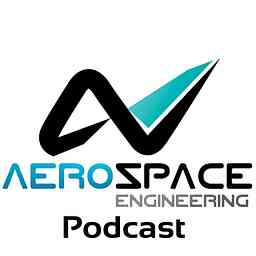
English
Popular podcast
Non-explicit
aerospaceengineeringblog.com
4.80 stars
37:32
It looks like this podcast has ended some time ago. This means that no new episodes have been added some time ago. If you're the host of this podcast, you can check whether your RSS file is reachable for podcast clients.
Aerospace Engineering Podcast
by Rainer Groh – Aerospace Engineer and ResearcherConversations with Aerospace Pioneers
Episodes
Podcast Ep. #29 – Samson Sky is Building the First Truly Useful Flying Car
56m · Published
Sam Bousfield is the founder and CEO of Samson Sky, a company that is developing the first truly useful flying car. Sam is an architect by training, but a passion for aviation led him to work on a supersonic aircraft with Boeing. Out of this experience came the idea of building a flying car called the Switchblade. Harking from an architectural background, Sam approached the problem of designing a flying car slightly differently. Rather than asking the question of how you could make a car fly, Sam and his team focused on the architectural question of how a vehicle that can both fly and drive should be designed. Answering this question led the Samson team to some unique design choices, such as a three-wheel layout and wings that stow and swing out from underneath the vehicle. One of the other challenges in designing a flying car is striking the right compromise between on-road and off-road performance. For example, a car should preferably create downforce, while a plane should create lift. To achieve this Samson Sky has made some very clever design choices in terms of the layout and shaping of the Switchblade, as well as the positioning of the wings and centre of gravity, and the use of lightweight composite materials. In our conversation, Sam and I talk about: why it has taken so long for a functional flying car to be built the main design challenges that need to be overcome the changes that need to be made to the vehicle when switching between flying and driving the way that Sam envisions the Switchblade to be used in practice and much, much more. If you enjoy the Aerospace Engineering Podcast you can support it by leaving a review on iTunes or by supporting it directly on Patreon, where patrons of the podcast receive exclusive behind-the-scenes content and special episodes. Thanks a lot for listening! This episode of the Aerospace Engineering Podcast is brought to you by my patrons on Patreon. Patreon is a way for me to receive regular donations from listeners whenever I release a new episode, and with the help of these generous donors I have been able to pay for much of the expenses, hosting and travels costs that accrue in the production of this podcast. If you would like to support the podcast as a patron, then head over to my Patreon page. There are multiple levels of support, but anything from $1 an episode is highly appreciated. Thank you for your support! This episode is also sponsored by StressEbook.com, which is an online hub for you if you are interested in aerospace stress engineering. StressEbook.com provides world-class engineering services and online courses on the stress analysis of aircraft structures, as well as a free ebook and blog. No matter if you’re a junior or senior structural analyst, stressEbook.com provides you with the skills and know-how to become a champion in your workplace. Selected Links from the Episode Samson Sky Webpage Samson Sky Youtube Switchblade Overview Slalom Test Wing Swing Mechanism NBC reports on the Switchblade's transforming tail
Podcast Ep. #28 – Natilus: the Startup Building Large Autonomous Cargo Drones
37m · Published
Aleksey Matyushev is the co-founder and CEO of Natilus, a startup headquartered in San Francisco. Natilus has set out to reduce global air freight costs through the use of large autonomous drones, and has moved quickly over the last couple of years to develop a sea-plane prototype to serve as a technology demonstrator. The engineers at Natilus are now moving ahead at full steam to design a land-based freighter drone based on a blended-wing body. As the name suggests, a blended aircraft has no clear demarcation line between wings and fuselage. Advantages of this approach are efficient lift generation aided by the wide airfoil-shaped body, allowing the entire aircraft to generate lift. This means that a blended wing body has better lift-to-drag ratios than a conventional aircraft, resulting in improved fuel efficiency. One particular challenge, however, is that a blended wing body does not feature a vertical and horizontal tail, and this makes controlling the aircraft particularly challenging. In this episode of the Aerospace Engineering Podcast, Aleksey and I talk about: his educational journey to becoming an expert aerodynamicist the technical details of the freighter drone Natilus is designing Natilus’ business model and near-term developments that are in the pipeline Last but not least, Natilus is currently hiring for a number of roles. So if you're interested in working for an innovative, fast-moving company, then head over to their website. If you enjoy the Aerospace Engineering Podcast you can support it by leaving a review on iTunes or by supporting it directly on Patreon, where patrons of the podcast receive exclusive behind-the-scenes content and special episodes. Thanks a lot for listening! This episode of the Aerospace Engineering Podcast is brought to you by my patrons on Patreon. Patreon is a way for me to receive regular donations from listeners whenever I release a new episode, and with the help of these generous donors I have been able to pay for much of the expenses, hosting and travels costs that accrue in the production of this podcast. If you would like to support the podcast as a patron, then head over to my Patreon page. There are multiple levels of support, but anything from $1 an episode is highly appreciated. Thank you for your support! This episode is also sponsored by StressEbook.com, which is an online hub for you if you are interested in aerospace stress engineering. StressEbook.com provides world-class engineering services and online courses on the stress analysis of aircraft structures, as well as a free ebook and blog. No matter if you’re a junior or senior structural analyst, stressEbook.com provides you with the skills and know-how to become a champion in your workplace. Selected Links from the Episode Natilus website Careers page Prototype test of sea-based drone Another interview with Aleksey Fast Company profile of Natilus
Podcast Ep. #27 – A Masterclass on Friction Welding with TWI’s Bertrand Flipo
36m · Published
In this episode I am speaking to Bertrand Flipo from The Welding Institute in Cambridge, UK. TWI Ltd has a long history of innovation in welding research, having been established as the British Welding Research Association in 1946. TWI Ltd is a world leader in research on friction welding and has been at the forefront of many modern friction welding processes. Briefly put, friction welding is a joining technique that does not melt the parts to be joined. Instead, two components are rubbed together to create heat through friction, and high pressure is then applied to squeeze the two pieces together. During this process the material plastically deforms and the high pressure causes the components to be fused together. Advantages of the process are fast joining times, typically on the order of a few seconds; relatively small heat-affected zones; and because friction welding techniques are melt-free, the material's microstructure can be maintained. I personally learned a lot during the recording of this episode, and Bertrand and his colleagues were very gracious to introduce me to the ins and outs of friction welding. So in this episode you will learn about: the differences between different friction welding techniques the main advantages of friction welding and the challenges to keep in mind some of the aerospace applications where friction welding is a game-changer and much, much more If you enjoy the Aerospace Engineering Podcast you can support it by leaving a review on iTunes or by supporting it directly on Patreon, where patrons of the podcast receive exclusive behind-the-scenes content and special episodes. Thanks a lot for listening! This episode of the Aerospace Engineering Podcast is brought to you by my patrons on Patreon. Patreon is a way for me to receive regular donations from listeners whenever I release a new episode, and with the help of these generous donors I have been able to pay for much of the expenses, hosting and travels costs that accrue in the production of this podcast. If you would like to support the podcast as a patron, then head over to my Patreon page. There are multiple levels of support, but anything from $1 an episode is highly appreciated. Thank you for your support! This episode is also sponsored by StressEbook.com, which is an online hub for you if you are interested in aerospace stress engineering. StressEbook.com provides world-class engineering services and online courses on the stress analysis of aircraft structures, as well as a free ebook and blog. No matter if you’re a junior or senior structural analyst, stressEbook.com provides you with the skills and know-how to become a champion in your workplace. Selected Links from the Episode TWI website Refill Friction Stir Spot Welding Friction Stir Welding of Lightweight Vehicles Linear Friction Welding Friction Welding of Blisks Friction Welding of Eclipse 500 Stringers TWI Youtube channel Slow Motion of Linear Friction Welding Refill Friction Stir Spot Welding Large-scale Friction Stir Welding
Podcast Ep. #26 – How AERALIS is Designing a New Family of Military Trainer Aircraft
21m · Published
On this episode I am speaking to Luca Leone who is the Head of Programme of AERALIS, a British startup designing a new class of military trainer and aerobatic jet aircraft. AERALIS have set out to re-invigorate the UK aircraft manufacturing sector with a military trainer that provides an exceptional pilot training experience. AERALIS' design is purposely modular meaning that a basic and an advanced version of the training aircraft are based on one common platform. This reduces costs in engine and airframe maintenance through training and spares commonality and also facilitates a shorter training period for pilots due to similarities between aircraft types. What’s more, AERALIS are developing a fully tailorable flying training system based on configurable cockpits and advanced simulators. In this way, AERALIS aim to not just be an aircraft manufacturer but a company that designs the total flying training experience. In this episode, Luca and I talk about: the features of the basic and advanced trainer aircraft the characteristics of the modular design the AERALIS training ecosystem and much, much more If you enjoy the Aerospace Engineering Podcast you can support it by leaving a review on iTunes or by supporting it directly on Patreon, where patrons of the podcast receive exclusive behind-the-scenes content and special episodes. Thanks a lot for listening! This episode of the Aerospace Engineering Podcast is brought to you by my patrons on Patreon. Patreon is a way for me to receive regular donations from listeners whenever I release a new episode, and with the help of these generous donors I have been able to pay for much of the expenses, hosting and travels costs that accrue in the production of this podcast. If you would like to support the podcast as a patron, then head over to my Patreon page. There are multiple levels of support, but anything from $1 an episode is highly appreciated. Thank you for your support! This episode is also sponsored by StressEbook.com, which is an online hub for you if you are interested in aerospace stress engineering. StressEbook.com provides world-class engineering services and online courses on the stress analysis of aircraft structures, as well as a free ebook and blog. No matter if you’re a junior or senior structural analyst, stressEbook.com provides you with the skills and know-how to become a champion in your workplace. Selected Links from the Episode AERALIS website Design Training Ecosystem AERALIS Experience podcast FlightGlobal article on AERALIS
Podcast Ep. #25 – Vertical Aerospace CCO Michael Darcy on the UK’s First Full-Scale eVTOL and the Growing Urban Mobility Market
26m · Published
Michael Darcy is the Chief Commercial Officer of the British eVTOL (electric vertical-takeoff-and-landing) company Vertical Aerospace. Vertical Aerospace has set out to change the way we fly short-haul distances and to reduce the time required for end-to-end journeys. Their vision is to develop an intercity air taxi service that gives customers the freedom to fly from local neighbourhood directly to the final destination. To achieve this, Vertical has assembled a world-class team with veteran engineers from Airbus, Boeing, Rolls Royce and leading Formula 1 teams to design a fully certified eVTOL aircraft starting from first principles. Since their founding in 2016, Vertical Aerospace has already built the UK's first full-scale eVTOL aircraft, and is iterating quickly to build the next generation of larger aircraft. One aspect that really stands out in this conversation is that Vertical Aerospace focuses strongly on quickly iterating through the design, manufacture and test cycle to improve their design in the most efficient way. In this episode, Michael and I discuss: Vertical's particular approach to designing eVTOL aircraft how Vertical Aerospace see the electric aviation sector developing and which hurdles need to be overcome by the industry to build certifiable aircraft If you enjoy the Aerospace Engineering Podcast you can support it by leaving a review on iTunes or by supporting it directly on Patreon, where patrons of the podcast receive exclusive behind-the-scenes content and special episodes. Thanks a lot for listening! This episode of the Aerospace Engineering Podcast is brought to you by AnalySwift. Do you work in the design and analysis of aerospace structures and materials? If so, AnalySwift’s innovative engineering software SwiftComp may be the solution you’re seeking. Used either independently for virtual testing of aerospace composites or as a plugin to power conventional FEA codes, SwiftComp delivers the accuracy of 3D FEA in seconds instead of hours. A general-purpose multi-scale modelling program, SwiftComp provides an efficient and accurate tool for modelling aerospace structures and materials featuring anisotropy and heterogeneity. SwiftComp quickly calculates the complete set of effective properties needed for use in macroscopic structural analysis. It also accurately predicts local stresses and strains in the microstructure for predicting strengths. Find out how others in composites are saving time while improving accuracy, considering more design options, and arriving at the best solution more quickly. A no-cost Academic Partner Program is now available for eligible universities. For a free trial, visit analyswift.com. SwiftComp: Right results. Right away. This episode is also sponsored by StressEbook.com, which is an online hub for you if you are interested in aerospace stress engineering. StressEbook.com provides world-class engineering services and online courses on the stress analysis of aircraft structures, as well as a free ebook and blog. No matter if you’re a junior or senior structural analyst, stressEbook.com provides you with the skills and know-how to become a champion in your workplace. Selected Links from the Episode Vertical Aerospace website Vertical Aerospace Youtube channel Flight footage Profiles by The Verge Flight Global
Podcast Ep. #24 – Veronica Foreman on Small Satellites and Virgin Orbit’s Air-Launched Rocket System
22m · Published
Veronica Foreman is a payload engineer at the small-satellite launch provider Virgin Orbit. Before starting her career at Virgin Orbit, Veronica earned several academic accolades including an Outstanding Undergraduate Researcher Award at Georgia Tech, and a Best Masters Thesis award at MIT. What I find especially impressive about her Masters work on small-satellite constellations is that Veronica considered both the design of constellations, as well as the economic and policy challenges to small-satellite mission success. As Virgin Orbit's mission is to be the premier dedicated launch service for small satellites, Veronica has seemingly found the perfect place for her expertise and passion. One of the key features of Virgin Orbit's launch design is its air-launching system that drops the rocket (LauncherOne) from the wing of a Boeing 747 (Cosmic Girl), providing a movable launchpad. As Veronica explains in this episode, this capability provides Virgin Orbit unique advantages in terms of providing a dedicated launch service for small satellites. In this episode of the Aerospace Engineering podcast, Veronica and I discuss: Virgin Orbit's vision the unique advantages and challenges of an air-launched rocket system some of Virgin Orbit's key engineering technologies and the growing importance of satellite constellations If you enjoy the Aerospace Engineering Podcast you can support it by leaving a review on iTunes or by supporting it directly on Patreon, where patrons of the podcast receive exclusive behind-the-scenes content and special episodes. Thanks a lot for listening! This episode of the Aerospace Engineering Podcast is brought to you by AnalySwift. Do you work in the design and analysis of aerospace structures and materials? If so, AnalySwift’s innovative engineering software SwiftComp may be the solution you’re seeking. Used either independently for virtual testing of aerospace composites or as a plugin to power conventional FEA codes, SwiftComp delivers the accuracy of 3D FEA in seconds instead of hours. A general-purpose multi-scale modelling program, SwiftComp provides an efficient and accurate tool for modelling aerospace structures and materials featuring anisotropy and heterogeneity. SwiftComp quickly calculates the complete set of effective properties needed for use in macroscopic structural analysis. It also accurately predicts local stresses and strains in the microstructure for predicting strengths. Find out how others in composites are saving time while improving accuracy, considering more design options, and arriving at the best solution more quickly. A no-cost Academic Partner Program is now available for eligible universities. For a free trial, visit analyswift.com. SwiftComp: Right results. Right away. This episode is also sponsored by StressEbook.com, which is an online hub for you if you are interested in aerospace stress engineering. StressEbook.com provides world-class engineering services and online courses on the stress analysis of aircraft structures, as well as a free ebook and blog. No matter if you’re a junior or senior structural analyst, stressEbook.com provides you with the skills and know-how to become a champion in your workplace. Selected Links from the Episode Virgin Orbit's homepage Technical details about the LauncherOne rocket Follow Virgin Orbit on Twitter Virgin Orbit YouTube channel Veronica on payload processing 2018 Highlights LauncherOne hot fire Veronica's MIT Master thesis on second-generation LEO satellite constellations
Podcast Ep. #23 – Samy Libsig on eXalt Aircraft’s Vision of Designing a New Breed of Sport Airplanes
32m · Published
Samy Libsig is one of the founders of the sport aircraft startup eXalt Aircraft Inc. eXalt currently comprises a team of three engineers that are bringing a unique combination of fresh design thinking and engineering experience to the world of sport airplanes. The vision of eXalt is to turn the sky into a playground with an aircraft that puts the pilot's flying experience in the foreground. This means an aircraft which is fun to fly, economical, maintenance friendly, and environmentally sustainable. Looking at the sport aircraft market, it is easy to notice that aircraft designs haven't evolved appreciably over the last couple of decades. This is probably for a good reason given that the laws of flying are obviously unchanged, and the design principles that worked in the past, are still valid today. But what is particularly fascinating is the manner in which eXalt Aircraft are using proven aerospace technologies and recombining them in novel ways to design an entirely modern aircraft. The result is an airplane that does not feature all of the most recent bells and whistles—just for the sake of using cutting-edge technology—but instead features a pragmatic design where each component has been carefully chosen to serve the company's vision of maximising the pilot experience. As you will hear in this episode, one of the best examples of this is eXalt's choice of a reinforced spaceframe design over an arguably lighter monocoque design. In this episode of the podcast, Samy and I talk about: the origins of eXalt their particular design philosophy some of the key design choices they have made and the near future of the company If you enjoy the Aerospace Engineering Podcast you can support it by leaving a review on iTunes or by supporting it directly on Patreon, where patrons of the podcast receive exclusive behind-the-scenes content and special episodes. Thanks a lot for listening! This episode of the Aerospace Engineering Podcast is brought to you by AnalySwift. Do you work in the design and analysis of aerospace structures and materials? If so, AnalySwift’s innovative engineering software SwiftComp may be the solution you’re seeking. Used either independently for virtual testing of aerospace composites or as a plugin to power conventional FEA codes, SwiftComp delivers the accuracy of 3D FEA in seconds instead of hours. A general-purpose multi-scale modelling program, SwiftComp provides an efficient and accurate tool for modelling aerospace structures and materials featuring anisotropy and heterogeneity. SwiftComp quickly calculates the complete set of effective properties needed for use in macroscopic structural analysis. It also accurately predicts local stresses and strains in the microstructure for predicting strengths. Find out how others in composites are saving time while improving accuracy, considering more design options, and arriving at the best solution more quickly. A no-cost Academic Partner Program is now available for eligible universities. For a free trial, visit analyswift.com. SwiftComp: Right results. Right away. This episode is also sponsored by StressEbook.com, which is an online hub for you if you are interested in aerospace stress engineering. StressEbook.com provides world-class engineering services and online courses on the stress analysis of aircraft structures, as well as a free ebook and blog. No matter if you’re a junior or senior structural analyst, stressEbook.com provides you with the skills and know-how to become a champion in your workplace. Selected Links from the Episode eXalt Aircraft's webpages eXalt's Twitter and LinkedIn profiles For angel investors: eXalt's AngelList profile
Podcast Ep. #22 – Mark Crouchen on Rockwood Composites and Manufacturing Complex Composite Components
28m · Published
Mark Crouchen is the managing director of Rockwood Composites, a company in the UK that specialises in manufacturing complex composite components using compression and bladder moulding. These manufacturing processes use fibre mats of carbon fibre, glass fibre, Kevlar, or any other material, which are pre-impregnated with a resin matrix and then placed in a mould, where they are cured at elevated temperature with the addition of external or internal pressure. The team at Rockwood has been supplying the aerospace, defense, medical and nuclear industries for over 25 years, with customers ranging from Leonardo Helicopters and the McLaren Formula 1 team to Safran and Facebook’s Aquila internet drone. In 2018, Rockwood won the Innovation in Manufacture award at the Composite UK industry event for their innovative use of advanced composite materials on the Tokomak ST40 nuclear fusion reactor. Composite materials have many benefits in terms of their excellent strength and stiffness at low weight. However, there is a common misconception that metal or ceramic components can easily be replaced one-to-one with composite components. The performance of any composite component is closely linked to the quality of the manufacturing process, and designing and manufacturing quality components is an area where Rockwood Composites particularly excel. In this episode of the podcast, Mark and I talk about: his background in engineering the types of structures that Rockwood Composites manufacture why composites manufacturing is a challenge and the special solution Rockwood found for the Tokomak ST40 fusion reactor If you enjoy the Aerospace Engineering Podcast you can support it by leaving a review on iTunes or by supporting it directly on Patreon, where patrons of the podcast receive exclusive behind-the-scenes content and special episodes. Thanks a lot for listening! This episode of the Aerospace Engineering Podcast is brought to you by AnalySwift. Do you work in the design and analysis of aerospace structures and materials? If so, AnalySwift’s innovative engineering software SwiftComp may be the solution you’re seeking. Used either independently for virtual testing of aerospace composites or as a plugin to power conventional FEA codes, SwiftComp delivers the accuracy of 3D FEA in seconds instead of hours. A general-purpose multi-scale modelling program, SwiftComp provides an efficient and accurate tool for modelling aerospace structures and materials featuring anisotropy and heterogeneity. SwiftComp quickly calculates the complete set of effective properties needed for use in macroscopic structural analysis. It also accurately predicts local stresses and strains in the microstructure for predicting strengths. Find out how others in composites are saving time while improving accuracy, considering more design options, and arriving at the best solution more quickly. A no-cost Academic Partner Program is now available for eligible universities. For a free trial, visit analyswift.com. SwiftComp: Right results. Right away. This episode is also sponsored by StressEbook.com, which is an online hub for you if you are interested in aerospace stress engineering. StressEbook.com provides world-class engineering services and online courses on the stress analysis of aircraft structures, as well as a free ebook and blog. No matter if you’re a junior or senior structural analyst, stressEbook.com provides you with the skills and know-how to become a champion in your workplace. Selected Links from the Episode Rockwood Composites Rockwood wins Innovation in Manufacture award Rockwood and fusion reactors
Podcast Ep. #21 – Prof. Paul Withey on Single-Crystal Superalloys for Jet Engine Turbines
29m · Published
Paul Withey is the Professor of Casting at the School of Metallurgy and Materials of the University of Birmingham, UK. Before joining the University of Birmingham in 2018, Paul worked at Rolls Royce for 21 years developing new superalloys and manufacturing processes for gas turbine components. As an Engineering Associate Fellow, Paul was a member of a select group of the top 100 specialist engineers across all engineering disciplines within Rolls Royce, and in 2015, Paul and his team were awarded the highest technical award within Rolls-Royce; the Sir Henry Royce Award. Paul’s particular expertise lies in investment casting of aerospace metals, especially of high-temperature superalloys used in the hot turbine stages of modern jet engines. Throughout his career at Rolls-Royce, Paul has developed and optimised manufacturing processes for single-crystal turbine blades with a total of 14 patents to his name. Despite phenomenal advances in materials technology, a number of questions with regard to how the turbine blade shape, materials and process parameters interact remain unanswered, and these questions form the basis of Paul’s ongoing research. In this episode, Paul and I discuss: the unique differences between research in academia and industry what single-crystal superalloys are and how they are manufactured why single-crystal superalloys are a critical technology for modern jet engines and the research questions that Paul is currently trying to answer If you enjoy the Aerospace Engineering Podcast you can support it by leaving a review on iTunes or by supporting it directly on Patreon, where patrons of the podcast receive exclusive behind-the-scenes content and special episodes. Thanks a lot for listening! This episode of the Aerospace Engineering Podcast is brought to you by AnalySwift. Do you work in the design and analysis of aerospace structures and materials? If so, AnalySwift’s innovative engineering software SwiftComp may be the solution you’re seeking. Used either independently for virtual testing of aerospace composites or as a plugin to power conventional FEA codes, SwiftComp delivers the accuracy of 3D FEA in seconds instead of hours. A general-purpose multi-scale modelling program, SwiftComp provides an efficient and accurate tool for modelling aerospace structures and materials featuring anisotropy and heterogeneity. SwiftComp quickly calculates the complete set of effective properties needed for use in macroscopic structural analysis. It also accurately predicts local stresses and strains in the microstructure for predicting strengths. Find out how others in composites are saving time while improving accuracy, considering more design options, and arriving at the best solution more quickly. A no-cost Academic Partner Program is now available for eligible universities. For a free trial, visit analyswift.com. SwiftComp: Right results. Right away. This episode is also sponsored by StressEbook.com, which is an online hub for you if you are interested in aerospace stress engineering. StressEbook.com provides world-class engineering services and online courses on the stress analysis of aircraft structures, as well as a free ebook and blog. No matter if you’re a junior or senior structural analyst, stressEbook.com provides you with the skills and know-how to become a champion in your workplace. Selected Links from the Episode Paul Withey's research profile A brief history of single-crystal superalloys Turbines stresses and turbine blade materials Modelling video of grain selection manufacturing Video about Rolls Royce turbine blades
Podcast Ep. #20 – Airbus Engineer Oliver Family on the E-Fan X Demonstrator
32m · Published
Oliver Family is the Overall Aircraft Design Leader of the Airbus E-Fan X demonstrator. The E-Fan X is a hybrid-electric technology demonstrator being developed by Airbus, Rolls-Royce and Siemens based on a British Aerospace 146 regional airliner. The driver behind the E-Fan X demonstrator is that current aircraft designs have converged to a near-optimum, and with existing technologies, it is difficult to meet the stringent sustainability goals in terms of CO2/NOX emissions and reductions in noise. New technologies, such as electrification, are therefore required to achieve these goals. As we have seen on other episodes of the podcast, electrification of aircraft is currently a hot topic with new start-up companies promising to disrupt and revolutionise the regional aircraft market. In this environment, one may assume that incumbents like Airbus are too slow to react to a changing technology landscape. As you will hear in this episode, nothing could be further from the truth. The E-Fan X project is structured as a separate entity within Airbus with the explicit mission of challenging Airbus’ legacy business. As you will hear, the consequences of integrating an electric propulsion system on a regional aircraft run much deeper than mere calculations about battery power density and battery longevity. In fact, it's the secondary effects that we rarely think, hear and read about, such as thermal management of batteries; the interaction between pilots and new control systems; and the challenges of new certification protocols, that are especially challenging. So in this episode, Oliver and I discuss: what exactly the E-Fan X demonstrator aims to achieve the main technical and economic challenges of electric aircraft and how electrification widens the design envelope for engineers If you enjoy the Aerospace Engineering Podcast you can support it by leaving a review on iTunes or by supporting it directly on Patreon, where patrons of the podcast receive exclusive behind-the-scenes content and special episodes. Thanks a lot for listening! This episode of the Aerospace Engineering Podcast is sponsored by SAMPE North America. SAMPE is a global professional society that has been providing educational opportunities on advanced materials for more than 70 years. SAMPE’s network of engineers is a key facilitator for the advancement of aerospace engineering by enabling information exchange and synergies between aerospace companies. To find out how SAMPE can help you learn more about advanced materials and process visit SAMPE's website, or consider attending one of SAMPE’s conferences, such as CAMX, the largest and most comprehensive composites and advanced materials event for products, solutions, networking, and advanced industry thinking. This episode is also sponsored by StressEbook.com, which is an online hub for you if you are interested in aerospace stress engineering. StressEbook.com provides world-class engineering services and online courses on the stress analysis of aircraft structures, as well as a free ebook and blog. No matter if you’re a junior or senior structural analyst, stressEbook.com provides you with the skills and know-how to become a champion in your workplace. Selected Links from the Episode Airbus announcement on the E-Fan X Airbus on the future and importance of electric flight (Link 1 and 2) Royal Aeronautical Society article on the E-Fan X Rolls Royce video on the E-Fan X engines
Aerospace Engineering Podcast has 50 episodes in total of non- explicit content. Total playtime is 31:16:50. The language of the podcast is English. This podcast has been added on August 6th 2023. It might contain more episodes than the ones shown here. It was last updated on August 6th, 2023 18:06.
Similar Podcasts
Every Podcast » Podcasts » Aerospace Engineering Podcast